Airbus A380a, combustible del cel
2004/02/01 Kortabarria Olabarria, Beñardo - Elhuyar Zientzia Iturria: Elhuyar aldizkaria
Dos motors a triar
Depenent de l'opció que realitzin les empreses que adquireixin l'avió, l'A380 podrà transportar dos tipus de motors, un de Rolls Royce i un altre de General Electric i Prat Whitney GP7000 Alliance. L'empresa ITP de Zamudio col·labora amb Rolls Royce en la fabricació del motor Trent 900.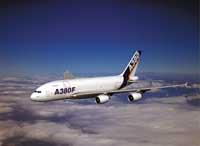
Queden dos anys perquè comencin els vols dels avions A380 d'Airbus. No obstant això, Airbus ja ha rebut encàrrecs per a realitzar més de 110 A380. No és d'estranyar, ja que tots els experts ho consideren substitut del Boeing 747.
Li han posat la següent targeta de presentació: “Avió A380: Tindrà capacitat per a transportar a 550 persones, serà tan ràpid com segur, consumirà molt menys combustible i gairebé no contaminarà el medi ambient i cobrirà l'augment de la demanda de viatjar amb avió”. Per descomptat, són paraules dels comandaments d'Airbus. No obstant això, és clar que la corona real aèria canviarà de memòria: El boeing 747 haurà de lliurar-ho a l'A380.
El nou Rei es presentarà amb nombroses novetats de molt diversa índole. El disseny serà nou, però es mantindran les característiques dels avions d'Airbus. És a dir, el gegant de tres plantes, per a dos passatgers i el subjacent per a carregar, tindrà una sèrie de característiques que tenien els avions petits. Per tant, la cabina dels pilots, els procediments de pilotatge de l'avió i les sensacions seran similars. Això significa que els pilots no necessitaran grans cursos de formació.
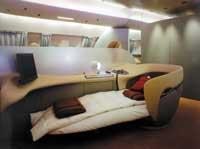
En materials, el nou avió també aporta novetats. L'A380 serà major que els avions actuals, però tindrà menys pes i millor aerodinàmica. Això evitarà el treball previ dels motors, la qual cosa reduirà l'ús de combustibles, reduirà les emissions a l'atmosfera i permetrà volar més barat.
El Glare serà el material més revolucionari que porta l'A380. El material Glare està format per fines capes d'alumini i fibres de vidre intercalades. Aquest material és més esponjós que l'alumini, de menor compacidad i pes, però més resistent i durador. Durant la realització dels tests es va esquerdar una làmina de glare, que després de completar milers de cicles de vol no va augmentar la fissura. També va reaccionar millor davant la corrosió i el foc que davant els materials convencionals.
El nou avió consta de nombroses peces de fibra de carboni reforçada, com la caixa sud que unirà les ales i el fuselatge és de fibra de carboni. Si s'hagués realitzat amb el millor aliatge d'alumini, tindria un pes de tona i mitja més. La caixa per al lema que condueix l'avió també es fabricarà amb aquest material. El 40% de l'estructura i de les peces es realitzaran amb fibres de carboni, aliatges metàl·lics lleugers i termoplàstiques.
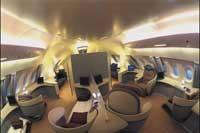
Com si la pèrdua de pes s'hagués convertit en una obsessió, a més de buscar materials més lleugers, els dissenyadors del nou avió d'Airbus han realitzat altres esforços. Un d'ells ha estat portar el centre de gravetat de l'avió cap endarrere. Amb aquest canvi, han guanyat 40 metres quadrats de sòl per a l'estabilitzador vertical i el seu corresponent pes, sense perdre per descomptat l'estabilitat.
Els canvis en els sistemes hidràulics també han suposat un menor pes dels avions. A causa de la major pressió d'aquests sistemes, els tubs i components hidràulics per a aconseguir la potència requerida per l'avió seran menors i menors. Els avions militars porten temps usant aquests sistemes de pressió i ja han demostrat que, malgrat estar sota la influència de la pressió, els fluids no es danyen. Després de tots els canvis, l'A380 tindrà 240 tones de pes, 10-15 tones menys que el 747.
A més de tenir un menor pes, s'ha tingut en compte la seguretat i l'estabilitat. El nou avió tindrà quatre sistemes de vol. L'avió podrà ser controlat per qualsevol d'ells, per la qual cosa si falla algun sistema, la resta romandran aquí.
Els autors de l'A380 han estès el respecte al medi ambient a quatre vents. Diuen que podrà transportar més passatgers però traient menys soroll i emetent menys emissions a l'atmosfera.
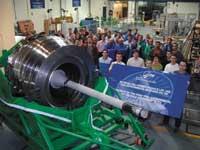
La reducció del soroll és conseqüència de la nova generació de motors, el disseny de les ales i la tecnologia i disseny del tren d'aterratge. Això permetrà a l'avió respectar tots els límits de soroll. Durant la seva estada en el sòl, l'A380 es desplaçarà amb dos motors, en lloc dels quatre, amb el que es redueix el soroll.
La reducció de l'atmosfera es deu a la disminució del consum de combustible. I és que aquest avió necessitarà 3 litres de combustible per cada 100 quilòmetres i passatger, el menor consum que han tingut fins avui els avions utilitzats en viatges llargs.
Una dels dubtes més importants que sorgeixen en la construcció dels seus grans avions és la relativa als aeroports, ja que no tots són capaços d'agafar avions de qualsevol grandària. Per això, abans del seu disseny, els tècnics d'Airbus han treballat amb 60 aeroports internacionals. En conseqüència, l'A380 és compatible amb les instal·lacions de molts aeroports actuals. Té grans ales, però això és més un avantatge que un inconvenient. Per això, i a causa de la potència dels nous motors, pot utilitzar pistes relativament curtes d'enlairament i aterratge. També l'ajuda el tren d'aterratge de 20 rodes principal, ja que la petjada que deixa l'avió és equivalent a diversos avions actuals, senyal que el pes es distribueix bé en vint rodes.
El nombre de passatgers que pot transportar l'A380 també ha provocat la col·laboració entre els aeroports i Airbus. Es necessiten grans sales d'espera per a 550 persones. El sistema d'evacuació de les 16 sortides d'emergència també és conseqüència directa del nombre de passatgers.
Innovació de processos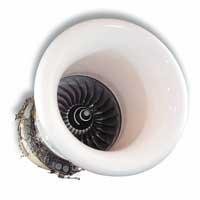
Com és evident, l'A380 d'Airbus serà un avió gran i nou basat en petits canvis. Aquestes petites adaptacions han suposat no sols la renovació de l'avió, sinó també la renovació del seu procés de fabricació. Una de les principals novetats és la pròpia organització del treball. Al voltant de 6.000 persones treballen amb el nou avió. Per a poder coordinar el treball de tantes persones s'ha implantat un sistema en línia. Atès que les dades estan en mans dels participants en el projecte, els canvis es poden realitzar de forma més ràpida, pas a pas, per a evitar sorpreses quan s'iniciïn els treballs de muntatge.
El gegant està construint amb noves tècniques de fabricació. Alguns d'ells han donat molt bon resultat i ja s'han incorporat als processos de fabricació d'altres avions. La soldadura per feix làser pot ser un bon exemple. Fins al moment, diversos trams del fuselatge s'unien mitjançant reblons, però en el cas de l'A380 s'està treballant en la soldadura per feix de làser. A més de reduir el pes, amb aquesta tècnica s'uneixen les parts de l'avió més ràpidament que amb els reblons, disminuint el risc de fissures.
A causa de la grandària de l'avió, algunes de les persones que treballen han hagut de realitzar alguns canvis en les seves instal·lacions i realitzar noves instal·lacions. Destaquen els de Tolosa i Hamburg, on es realitzaran els últims muntatges.
A Tolosa, prop de l'aeroport de Blagnac, estaven finalitzant al desembre les instal·lacions amb una superfície de 50 hectàrees. Allí han realitzat, entre altres, els camps de proves estàtiques i el muntatge final. La zona té una longitud de 490 metres, una amplària de 250 metres i una altura de 46 metres, la qual cosa equival a 20 camps de futbol. Prop d'aquest lloc s'ha construït un edifici de 19.000 metres quadrats per a acollir el simulador de la cabina A380 i altres sistemes.
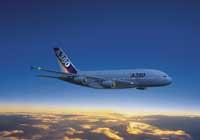
A Hamburg es va començar a condicionar una superfície de 140 hectàrees al novembre de 2001. L'edifici principal, hangar de muntatge, es va inaugurar al maig de l'any passat. L'edifici té 228 metres de longitud, 120 metres d'amplària i 23 metres d'altura. Aquí es munten la part davantera i posterior del fuselatge i els sistemes bàsics de vol. També s'han construït nous edificis a Gal·les, hangars a Getafe i Puerto Real, tallers a Nantes, Saint Nazaire…
El transport ha donat als d'Airbus tants maldecaps com la construcció de nous edificis. El muntatge final es realitzarà a Tolosa. Allí formaran l'avió gegant, però moltes de les parts que s'han d'emportar són massa grans per als mitjans de transport habituals i han hagut d'inventar noves, com les gabarras especials. Les parts de l'avió s'emportaran per mar, carretera i riu. Quan l'avió es completa amb el puzle dels episodis, recorrerà els cels d'allí i d'aquí, realitzant llargues rutes.
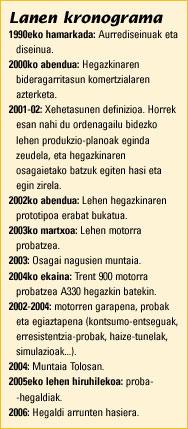
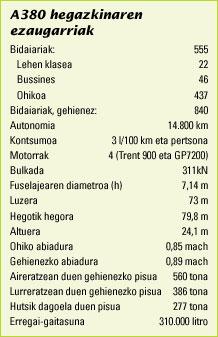
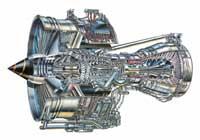
El motor 900 és l'últim de la família dels motors Trent de Rolls Royce. La primera cria d'aquesta família de motor, el motor Trent 700, va néixer fa 25 anys. Les creacions posteriors s'han basat en les seves característiques. La família Rolls Royce ha estat un èxit, ja que s'han fet milers. Segons els britànics, aquests motors han aconseguit guanyar el 80% dels quals han entrat en la competició de compra.
El nou motor dissenyat per Rolls Royce té tres eixos: el d'alta pressió, l'intermedi i el de baixa pressió. En ITP fabriquen una turbina de baixa pressió que suporta la menor pressió i temperatura a l'interior del motor. The turbine at baixa pressure moves the turbine through a pivot. La turbina té un diàmetre de dos metres, dividida en cinc etapes que conformen els àleps i l'estructura fixa, encara que és menor que la del motor GP7000, que té sis etapes.
El motor Trent 900 es basa en tres eixos. Segons l'enginyer d'ITP Bittor Olabarria, aquest motor conjumina sota pes i alta eficiència alhora, “amb baix consum, sota cost i baix soroll”. El muntatge complet dels motors es realitza en el mateix Rolls Royce, a Gran Bretanya, i ITP ja ha començat a fer passos en la fabricació de les turbines d'aquest motor. Les peces de les turbines es realitzaran en Zamudio per al seu posterior muntatge en Ajalvir de Madrid. ITP haurà de lliurar les turbines en el Rolls Royce, en el Derby anglès, que és l'encarregat de lliurar-les.
Segons Olabarria, en qualsevol motor el pes és un factor molt important i en alguns casos pot arribar a tenir límits. La versió més pesada del motor Trent té uns 5.900 quilos, mentre que el motor de General Electric i Pratt Whitney té 100 quilos més. No obstant això, el motor GP 7000 de General Electric i Pratt Whitney té altres característiques favorables. “Això és un motor de dos eixos, per la qual cosa pot ser més econòmic i, en teoria, necessita menys manteniment”.
La relació eficiència/consum del motor també diu molt a favor o en contra d'un motor, però el límit real en el desenvolupament d'un motor és el soroll. “Un motor pot tenir major o menor consum, millor o pitjor eficiència i evolucionarà o retrocedirà amb el que té. Amb el compte de soroll no hi ha marge. Les restriccions són cada vegada més nombroses i les limitacions que s'imposen no poden ser superades. Per a acostar-nos a aquests objectius hem hagut d'utilitzar noves tecnologies”.
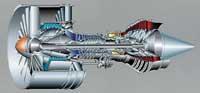
Els Rolls Royce han aconseguit reduir el soroll augmentant el diàmetre de la turbina en 13 centímetres, reduint així la velocitat de sortida del gas i provocant el soroll del motor. A l'ésser el motor Trent 900 de Rolls Royce, també és responsable del soroll que pot generar el motor. No obstant això, també han hagut de col·locar la seva pedres en ITP. “Com s'ha comentat anteriorment, des del punt de vista del soroll, els avions tenen grans limitacions. Nosaltres també hem fet esforços per a reduir el soroll i introduir-lo en els límits, encara que la part menys sorollosa dels motors sigui la mateixa turbina. El component més sorollós és el ventilador davanter”.
Per a poder fer la turbina han hagut de fer coses noves, treballar en equip i superar reptes. “Una d'elles correspon a l'aerodinàmica de la turbina, ja que hem realitzat un disseny aerodinàmic 3D perquè el motor sigui més eficient. S'han realitzat importants canvis en el disseny: optimització de discos, carcassa, refrigeració, rodaments de l'estructura, etc. Pel fet que la temperatura a l'entrada de la turbina és de 1.000 °C, s'han hagut d'emprar aliatges de níquel. La majoria dels materials han estat fosos i forjats amb exigents requeriments de qualitat. La mecanització d'aquests materials no és fàcil, ni la soldadura ni el conformat, pel fet que les toleràncies per pes són molt petites. Hem hagut de realitzar nombroses recerques i desenvolupaments”.
Malgrat la importància d'aquests detalls, segons Bittor Olabarria, el major repte per a ITP ha estat la grandària dels components del nou motor, ja que els criteris utilitzats en les turbines que s'han realitzat fins al moment eren o no sabien. No se sap fins a provar-ho i així es va abordar en ITP.
El mecanitzat i fabricació de discos de turbina, suports posteriors, carcassa de la turbina, àleps estàtics, rodaments per a suportar l'estructura i altres components s'ha realitzat per primera vegada en Zamudio. Per a poder fer les peces han hagut de comprar màquines, aprendre a usar-les, i aprendre a fer els ingredients. El procés té més dificultats de les que sembla. “En els components de l'aviació les toleràncies són molt importants i difícils, ja que el material que utilitzem, a més de lleuger, és dur. Per tant, hem hagut de fer un treball de mecanitzat molt fi, millorant i afinant el procés de fabricació”.
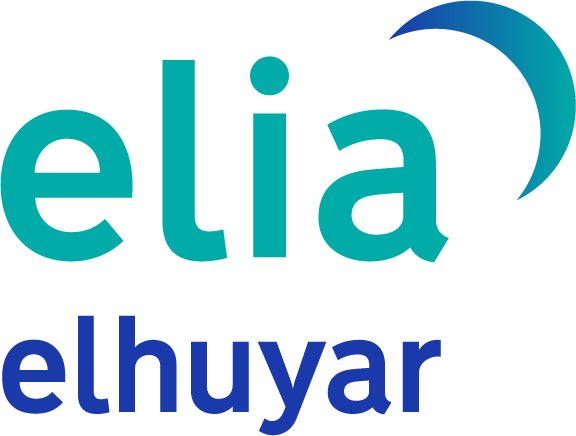
Gai honi buruzko eduki gehiago
Elhuyarrek garatutako teknologia