Hierro, metal preciado
2003/07/01 Rementeria Argote, Nagore - Elhuyar Zientziaren Komunikazioa Iturria: Elhuyar aldizkaria
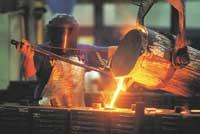
La importancia de la siderurgia en Euskal Herria no es puesta en duda por nadie. Tanto en la actualidad como en los dos siglos anteriores ha sido sin duda uno de los pilares de la economía vasca. Indirectamente, los altos hornos han influido en ámbitos tan diversos como la ordenación del territorio, los movimientos sociales, etc. Más de uno dirá que el hierro ha contribuido a cultivar el carácter de los vascos.
Pero la historia de la siderurgia no comenzó con los altos hornos en Euskal Herria, viene mucho antes. Antes se extraía el hierro en las ferrerías y antes en las eólicas.
A pesar de que la técnica de los vientos y las ferrerías era básicamente la misma, en las ferrerías se obtenía una mayor producción, ya que utilizaban la fuerza del agua de los ríos y arroyos para mover los fuelles, lo que permitía obtener una temperatura más alta en el horno gracias al viento soplado por los fuelles. En los vientos, por el contrario, los ferrones afectaban a los fuelles por la fuerza de sus brazos, por lo que la temperatura del horno dependía de la fuerza utilizada al accionar los fuelles.
Obtención de hierro puro
A pesar de que el hierro es muy abundante en la naturaleza, se encuentra principalmente en forma de óxido (mineral de hierro), por lo que en las ferrerías había que utilizar una reacción de reducción para separar el hierro puro del oxígeno y del resto de los elementos. En esta reacción el reductor era monóxido de carbono y se obtenía calentando el carbón con el aire de los fuelles.
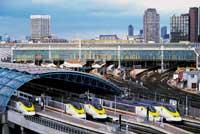
Química no es un proceso simple. La reacción del carbono con las moléculas de oxígeno del aire produce dióxido de carbono. Esta reacción es muy exotérmica, es decir, desprende mucho calor. El dióxido de carbono reacciona con el carbono y se obtiene monóxido de carbono. El monóxido de carbono actúa como reductor: reduce los óxidos de hierro y proporciona hierro puro.
El mineral de hierro utilizado en las ferrerías era mayoritariamente hematites (Fe 2 O 3). Sin embargo, es difícil reducir completamente el hematites, por lo que aparecen restos de magnetita (Fe 3 O 4) y wüstita (FeO) junto con el resto de impurezas. Estos óxidos de hierro aparecen como productos de reacciones intermedias para la obtención de metal puro.
Los ferrones trituraban el mineral de hierro antes de meterlo en el horno, aumentando así la superficie de reacción y facilitando la llegada del monóxido de carbono al óxido. Posteriormente, el carbón vegetal y el mineral triturado se introducían en el horno.
Para que se produjera esta gran cantidad de reacciones era imprescindible conseguir temperaturas elevadas en el horno. El horno se calentaba hasta unos 1.400 ºC, cerca de la temperatura de fusión del hierro (1.538 ºC), a la que se mantenía durante cinco o seis horas. Para ello tenían que añadir carbón sin cesar. Por ello, ante problemas en el suministro de carbón, muchas ferrerías tenían que dejar de trabajar.
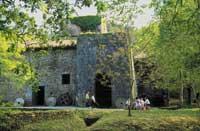
Por encima de 1.100 ºC se funden todos los compuestos distintos del hierro. Para aprovecharlo, los hornos tenían una traviesa que les permitía sacar las impurezas fundidas fuera del horno. Así explicado, la separación de hierro e impurezas parece sencilla, pero desgraciadamente la temperatura del horno no era homogénea y algunas impurezas (escorias) quedaban adheridas al hierro formando un más. Para liberar el hierro puro de la escoria, golpeaban el mazo con el mazo.
¿Por qué el hierro?
El hierro revolucionó la historia del metal, pero no fue un día. Además, debido a que la extracción de hierro requiere una temperatura muy alta, que debe mantenerse durante mucho tiempo, la tecnología requerida en el campo del metal era muy avanzada.
Cuando se consiguió la extracción de hierro, se consiguió el metal más duro conocido hasta entonces. Por ello, no es de extrañar que los romanos explotaran varios minerales de Euskal Herria, ya que uno de los pilares del imperio romano era el hierro. Asimismo, los romanos fueron los que mayores avances experimentaron en la industria siderúrgica. Pero antes, a. C. VI. Para el siglo XX, los vascos extraían el hierro, supuestamente enseñados por los celtas.
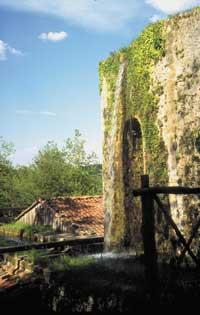
Los avances en la siderurgia llegaban por toda Europa. Se ha observado que las nuevas técnicas se propagaban rápidamente, ya que los restos más antiguos de los avances encontrados en todo el continente corresponden casi a la misma época. Pero en aquella difusión de la tecnología hay una excepción llamativa: XV. En el siglo XVIII se inauguró el alto horno. Con este novedoso método de extracción de hierro se obtenía un mayor rendimiento, pero en el País Vasco no se debía adoptar esta técnica. A pesar de que en casi todo el continente se utilizaba el horno alto, en Euskal Herria se siguió utilizando el horno de abajo en el siglo XIX. Hasta el siglo XX.
Se puede pensar que tenían motivos fundados para mantener la siderurgia tradicional. Una de ellas era la calidad del hierro producido. En Euskal Herria tenían materias primas muy adecuadas: En las minas de la zona de Somorrostro se extraía mineral o mineral rico en hierro, con cerca del 60% de hierro; además, el carbón vegetal utilizado como combustible era único, principalmente de madera de haya, y por si fuera poco, los puertos de transporte de hierro al exterior estaban cerca de las ferrerías y los marineros vascos eran experimentados.
Sin embargo, cuando entró el horno alto, las ferrerías dejaron de trabajar, la siderurgia tradicional se perdió y el tiempo fue eliminando las huellas.
Ferrería de Agorregi
Con el objetivo de conocer mejor aquella época tan importante de nuestra historia, se ha tratado de recuperar el trabajo de las ferrerías. Para ello se han catalogado y restaurado numerosas ferrerías. Así es el trabajo realizado por Arkeolan en la ferrería Agorregi de Aia.
El documento más antiguo de la ferrería de Agorregi es el XV. A pesar de su siglo XX, el edificio que hoy se puede ver restaurado es de XVIII. Lógicamente, el trabajo inicial en el proceso de recuperación fue la recogida de datos, ya que la documentación y el análisis de textos históricos son la base de la arqueología. Pero el equipo de Arkeolan fue un paso más adelante en Agorregi, donde se puso en marcha la ferrería y, siguiendo el antiguo método, consiguieron extraer el hierro. Este tipo de trabajos se denominan arqueología experimental y el programa utilizado en Agorregi se convirtió en un modelo de trabajo en la arqueología experimental internacional.
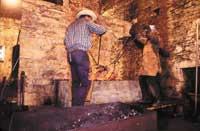
El trabajo posterior a la documentación fue la obtención de materias primas. Pero, ¿cómo conseguir carbón vegetal y mineral de hierro como los de antaño? La suerte tiene que ser a favor, sin duda. Tomaron el mineral de un barco hundido que apareció en la desembocadura del río Oria y que, al parecer, procedía de Somorrostro para abastecer a Agorregi y otras ferrerías cercanas. Por su parte, el carbón vegetal fue obtenido de las pruebas que se realizaron en Zerain para recuperar el trabajo de los carboneros.
Al mismo tiempo, se reformará el edificio y se instalarán canales, antenas, etc. tuvieron que limpiarse. Cuando todo estaba listo comenzaron las sesiones de extracción de hierro. Sin embargo, como el proceso y el utillaje no estaban descritos con exactitud, tuvieron que realizar más de un ensayo, introduciendo mejoras en cada prueba para corregir los errores.
Se dieron cuenta de que la de Agorregi era una ferrería inusual. El nombre de Agorregi proviene de Agorria, un topónimo que indica que se trata de un medio seco. Y probablemente se debe al caudal variable de los arroyos de la zona. Sin embargo, la puesta en marcha de los fuelles requiere veinte litros de agua por segundo y más para mover el martillo. Con el objetivo de hacer frente a este flujo de agua variable, la ferrería cuenta con tres embalses y dos cuestas, tecnología y arquitectura muy peculiares. siglo.
Estudio hidrogeológico para la viabilidad de la ferrería. Así supieron que tenían suficiente trabajo para ponerlo en marcha entre mayo y septiembre, y que en invierno, si no llueve a menudo, la ferrería se paraba. Por tanto, la ferrería de Agorregi no tuvo mucho éxito en la fabricación del hierro, pero es un valioso patrimonio para arqueólogos e historiadores contemporáneos.
Edad del Hierro
La extracción del hierro supuso una revolución en la industria del metal en la Edad del Bronce, más dura que el metal más fuerte conocido hasta entonces, el bronce. Dadas las ventajas de la utilización del hierro, la siderurgia se extendió con facilidad. Y la Edad del Bronce se trasladó a la Edad del Hierro.

El origen de la Edad del Hierro se sitúa en Asia Menor. Hacia 1200 años, aproximadamente durante la guerra de Troya. Sin embargo, todavía no está claro dónde y cuándo se produjo la primera extracción de hierro. Parece que la extracción de hierro se consiguió en diferentes lugares a la vez, como en Europa, Asia Menor y China.
También en África a. C. Muchos pueblos eran capaces de extraer hierro para el siglo V, utilizando pequeñas ferrerías.
La siderurgia adquirió gran fuerza en la India y fue uno de los mayores productores de hierro de la Antigüedad, prueba de ello fue Delin, a. C. Hay una columna de hierro de 400 años.
Desde entonces el hierro no ha perdido protagonismo y es una de las materias primas más utilizadas hoy en día. ¿Quién podría decir que terminó la Edad del Hierro?
Maldición del hierro
Según la Leyenda de Sisifo, los dioses Sisisifo le condenaron a subir una gran piedra hasta la cima y cada vez que intentaba en ella la piedra caía una y otra vez a la ladera.
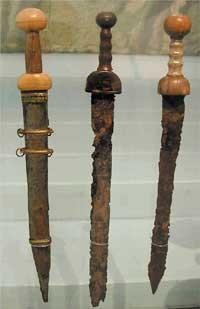
Algo parecido ocurre con el hierro: a pesar de que a partir de los óxidos de hierro se obtiene hierro puro, tiende a volver a oxidarse. Esto se debe a que el óxido es más estable que el hierro puro.
El hierro se oxida en contacto con el aire o el agua, ya que los átomos de hierro tienden a unirse a los átomos de oxígeno formando óxidos de hierro.
Con el objetivo de hacer frente a esta maldición, en aquella época experimentaron diversas aleaciones para obtener metales que se oxidaban con más facilidad mezclando hierro con otras sustancias.
En la actualidad, los útiles y objetos de hierro se pintan, untan con grasa o se recubren de plástico para evitar contacto directo con el aire o el agua. Otra forma de proteger el hierro es ponerlo en contacto con un metal que se oxida más fácilmente.
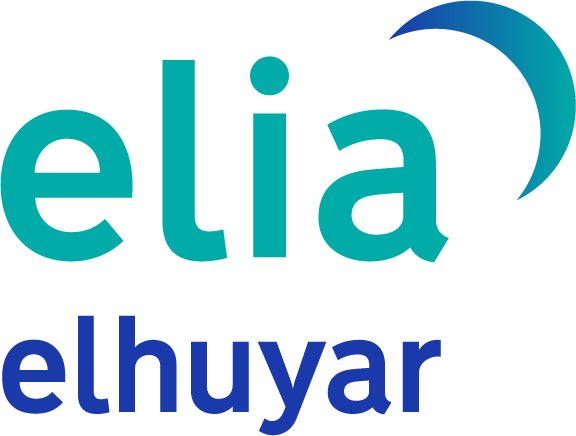
Gai honi buruzko eduki gehiago
Elhuyarrek garatutako teknologia