Additive manufacturing: new mentalities in engineering
2021/09/21 Elhuyar Zientzia Iturria: Elhuyar aldizkaria
Additive manufacturing starts from 3D design and builds parts without any kind of mold. With increasingly surprising materials. In this way, 3D printing has broken with the usual rigid engineering designs and parts and has brought new mentalities to industrial production. Experts talk about complete freedom of design, and BRTA researchers have highlighted that engineering is slowly being implemented.
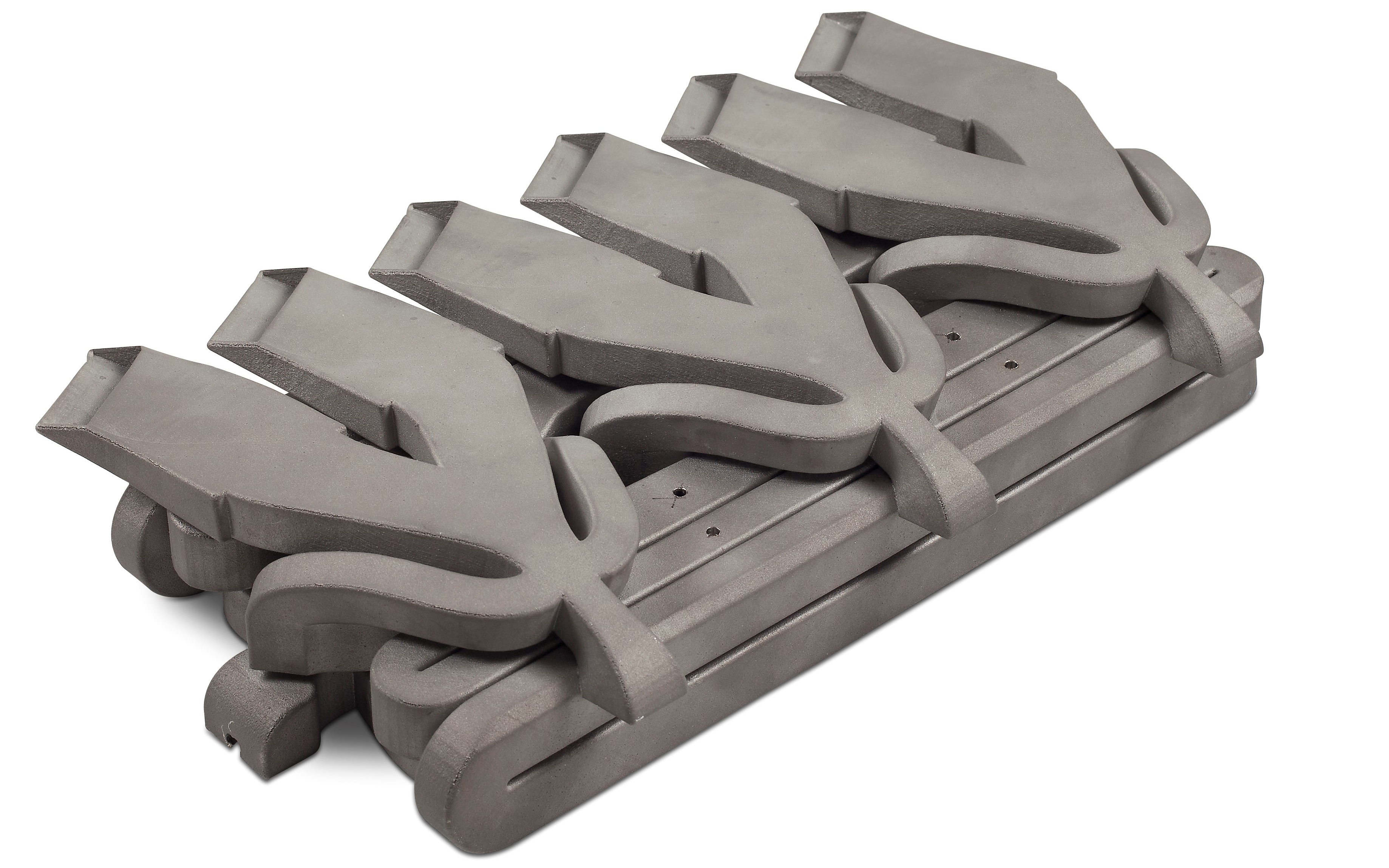
“Beyond the designs we consider to be common in engineering, additive manufacturing allows you to easily create parts with more organic designs inspired by trees or leaves. We call it bionic parts. You can create almost any complex design. The traditional industry is not used to designing them, but it will have to integrate them into its thinking,” says María San Sebastián Ormazabal. Lortek is a researcher at the technology center and collaborates with the other BRTA centers in the research and industrial implantation of additive manufacturing.
It's a manufacturing with great freedom of design. The piece comes from a simple digital design. Polymer 3D printers are the simplest example of additive manufacturing. But in industry, in addition to polymers, any kind of raw material is used: metals, ceramic materials, both hard and soft, porous, edible...
“Additive manufacturing has the advantage of making much better use of raw materials,” explains San Sebastian. “In conventional manufacturing, by subtraction, the material is extracted to the piece until the remaining material is removed and the desired geometry is achieved. In additive manufacturing, however, it is the reverse: the material is added only where the piece needs. Therefore, almost 100% of the raw material is used. In addition, as there is no need for turning, milling, forging, rolling, etc., the manufacturing process is simplified and much less energy is consumed. In one sense, it is a step towards the circular economy,” believes Nerea Ordás Mur, researcher at the Ceit Center, member of BRTA.
“Until the introduction of additive manufacturing, there were very complex geometry parts that could not be manufactured with conventional technologies. For example, those with internal channels. You had to make foundry, drill holes, then solder to add the pieces, drill to make another channel ... They were very complex and expensive operations. Now they get much faster,” explains Ordás.
Materials à la carte
Additive manufacturing has already been implemented in industry. It has entered, above all, aeronautics and the car. “One of the great challenges for the future is to be able to produce hundreds of thousands of serial units. On the other hand, the increase in the size of the parts that are manufactured, which is currently limited by the size of the equipment. But there are also interesting challenges in materials. Additive manufacturing can produce new materials that cannot be manufactured conventionally. This technology mainly uses two types of raw materials: dust and yarn. In the case of metallic powders, a lot of specific materials are being designed for this type of manufacturing. Sometimes, traditional materials are not the most suitable for this process and must be adapted to obtain better benefits and properties,” explains Ordás.
“Anyway, I think there is a more social challenge: education,” added San Sebastian. “That is, you have to introduce this technology into the thinking of people who are thinking about new pieces, so that they start to think about how innovative parts will conceptualize.”
Although new technology has started to be introduced in industry, research needs to be supported. “In Ceit, for example, we work a lot on the design and creation of materials. Being our steel and machine tool tradition, we mainly design metallic materials: steels, aluminum alloys, nickel alloys… But we also work in ceramics as technical ceramics with very special properties. BRTA research centers, together, can develop the entire value chain of additive manufacturing, from the design and manufacture of powders to the development of final parts treatments,” says Ordás.
_1_galeria.jpg)
“In post-processing we also have a lot of activity. These parts that come out of the printer, in most cases, are not willing to install them directly in the car or anywhere. We work on developing more suitable post-printing treatments such as thermal treatments.”
They have specialized in the different printing processes of Lortek. “We have several technologies to print,” says San Sebastian. “On the one hand, the manufacture based on sedimented powder bed, where the raw material is metallic powder and layer by layer makes the laser layer only integrate the previously defined area; and on the other hand, the direct implantation processes, where the raw material, in the form of powder or yarn, is deposited on a base until 3D piece is obtained.”
Partnership, strength
BRTA centers support companies when they decide to implement these technologies and are optimizing printing parameters. For both researchers, one of the strengths of BRTA is that virtually all centers investigate additive manufacturing technologies and processes. “On the other hand, there is great knowledge in machine tool, programming and auxiliary elements of robots. In short, the work of adding and founding the material must be performed by a robot in a synchronized way. I mean, it's also smart manufacturing. Our knowledge in Euskal Herria gives us a lot of strength,” says San Sebastian. Additive manufacturing will provide new engineering grip.
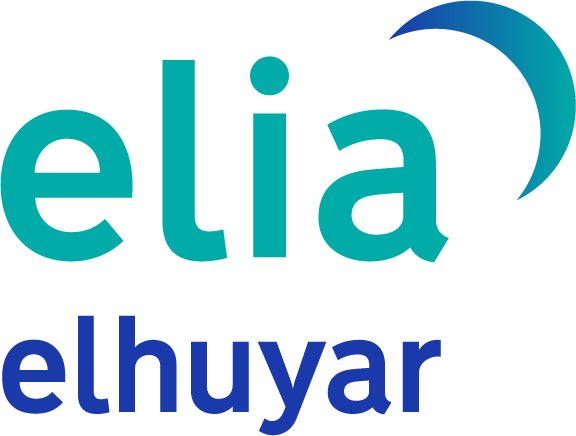
Gai honi buruzko eduki gehiago
Elhuyarrek garatutako teknologia