Catching reflexes
2008/05/01 Álvarez Busca, Lucía - Elhuyar Zientziaren Komunikazioa Iturria: Elhuyar aldizkaria
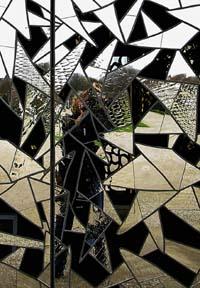
As the Chinese, Greeks, Etruscans and Romans developed the mirrors softening the bronze. For centuries bronze was the most important material for creating mirrors. So it was in modern times until two Muran artisans changed it and got the first glass mirrors. The work of these Muran artisans was undoubtedly the greatest revolution in the manufacture of mirrors.
The Murano Revolution
The basic idea was the same as the background: use metal to get reflections, but in much smaller amounts. Muran artisans began to work glass centuries ago. Two of them obtained a soft and flat glass, and on their back applied a thin layer of a metal with reflective capacity. It was a real revolution.
It became a very exclusive product. On this way of making the mirrors there arose a guild in Murano, for whose manufacture glass and metal composition were secret; if the secret was counted it was punished with the death penalty.
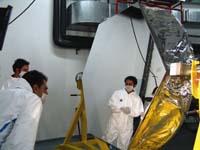
Since then, this has been the basic technology of mirrors: polished glass and a metal layer. However, the metals used in the manufacture of the reflective coating have changed. XVIII. In the twentieth century mercury was used, as it is a metal with large reflective capacity. But due to the toxicity of mercury, those who made mirrors suffered vibrations, depression, confusion, insomnia and memory loss, among others. Therefore, over time, mercury was replaced by other metals such as gallians or Indians.
XIX. In the eighteenth century a new revolutionary step is taken in the manufacture of mirrors, beginning to use silver. German chemist Justus von Liebig discovered that silver was very appropriate. It returns 97% of the light it receives between red and green light, that is, most of the visible spectrum. For these properties, in 1857, Jean Focault first used silver for telescope mirrors. Currently, most of the mirrors in the houses are made in silver, although a few are made in copper or aluminum.
Faithful reflection
The common mirrors have the same structure as those invented in Murano. In precision mirrors, however, the structure is inverse. To prevent the glass from diverting light, the metal layer is applied to the mirror holder. Since the light does not have to cross the glass, the rays are not diverted by it.
Such mirrors are used on telescopes, for example. In fact, the rays of light projected by the stars barely reach the ground. In order for these stars to be seen as best as possible, a mirror capable of capturing large amounts of light is necessary.

www.flickr.com/
photos/Lordferguson)
A perfect mirror theoretically reflects 100% of the light it receives. At the moment, the best dielectrics reflect 99,998% of the light for different wavelengths. For example, lasers of certain colors reflect them in a very concrete way.
In addition to the right materials, the mirror should be smooth to be precise. In the polishing operation silicates are used, since the glasses are composed of silicate and are corroded with products of similar composition. First, with highly corrosive products, silicon oxide glass is shaped. To bring a little closer the necessary shape is used aluminum oxide and finally an iron oxide to leave the surface as smooth as possible. This process has been done manually for a long time. And although very precise smoothness is now achieved through machines, in many cases the final polishing is done manually.
Non-fractional mirror
They also invented a parabolic mirror without polishing: a liquid mirror. When turning a liquid, its surface takes the shape of the parable. In them, as in solids, a metal is used to reflect, but as the name suggests, the metal is in a liquid state.
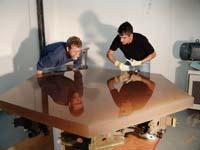
Mercury, the only liquid metal at room temperature, is used for liquid mirrors, but it is also being investigated whether indio-gallium eutectic alloys can be used for this work. The liquid metal is poured into a bowl that rotates at constant speed. The metal surface is expected to stabilize, and the liquid surface adopts the shape and capabilities of a mirror.
High-pressure air injectors are used to turn the mirror. Unfortunately, these structures cannot withstand very heavy structures, which limits the diameter of the liquid mirrors that can be obtained. Therefore, it is necessary to build a container with a limited weight and use as few metals as possible. Parabolic containers are constructed, allowing the use of very thin layers of mercury of only 1 or 2 mm.
They have a problem. Liquid mirrors are necessarily cenital, that is, they look up and cannot move through that position. They do not support oscillations nor can they be moved from place to angle. This limits the use of these mirrors. And, at the same time, the size of the mirror is a limit. Theoretically, liquid mirrors up to 15 meters can be obtained, although these measures have not yet been reached. The largest liquid mirror currently available is in Canada. The Large is a 6-metre diameter Zenit Telescope primary mirror.
Dividing, higher
The larger the mirrors, the more accurate the images are. But, as in liquids, in solids there are technical limitations for the manufacture of large mirrors.
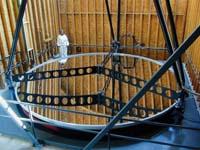
But you can also make segmented mirrors. In fact, the union of many 'small' hexagonal mirrors exceeds eight metres in diameter. Thus, each segment is within the limit of the aluminizing machine. Currently, the largest segmented mirror is being built in the Canary Islands. The primary mirror of the Gran Telescopio de Canarias will have a diameter of 11.3 meters and will consist of 36 hexagonal mirrors.
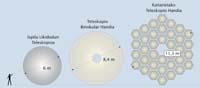
Segmented mirrors will allow to build larger and larger mirrors. At the European Southern Observatory (ESO), together with European companies and universities, they want to build a segmented 100-metre diameter mirror to be used on a telescope. The project, known as the ELT (Extremely Large Telescope), would undoubtedly be the largest mirror of a telescope. And, of course, the largest in the world.
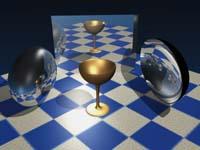
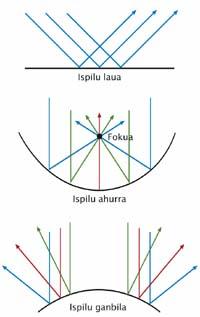
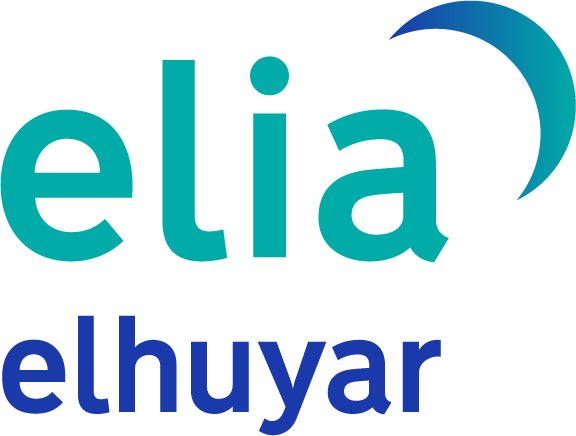
Gai honi buruzko eduki gehiago
Elhuyarrek garatutako teknologia