Kentzetik gehitzera: metalak metatzen
2025/03/01 Aldalur Urresti, Eider - Tecnaliako ikertzailea, Ingeniaritza Mekanikoan doktorea Iturria: Elhuyar aldizkaria
Historian zehar, fabrikazio-teknologiak eta industria, oro har, garatzen joan dira, gaur egun mundu mailan metalen industriaren zutabe nagusiak diren galdaketa-, konformazio- eta mekanizazio-teknologietara iritsi arte. Azken urteetako aurrerapen teknologikoei esker, fabrikazio-teknologia berritzaile bat gaineratu behar zaio zerrenda horri: fabrikazio gehigarria.
Gizakiak sortutako lehen harrizko tresnen aztarnek 3,4 milioi urte atzera garamatzate, Harri Arora. Garai hartan, gizakia lehendabizikoz harriak lantzen hasi zen, elkarren kontra kolpatuz, erauzketa bidez ertz zorrotzeko tresnak, armak eta puntak fabrikatzeko. Eta, hala, gaur egungo mekanizazio-teknologien lehen aurrekaria ezarri zen. Jarraian, Neolitoan, harria artefaktuak fabrikatzeko oinarrizko elementu gisa erabiltzeari utzi zitzaion, eta metalak lantzeari ekin; hasieran, hotzeko mailukatzearen bidez (egungo konformazioaren aitzindaria), eta, ondoren, mineralen galdaketa erabilita (galdaketa modernoaren aitzindaria).
Paleolitoan gizakiak mekanizazio modernoaren lehen harria jarri zuenetik, fabrikazio-teknologia horiek garapen handia izan dute, 1. irudian ikusten den bezala. Bide horren lekuko da, adibidez, Michelangelo Buonarroti pizkundeko eskultore eta margolari italiar handiak 1501-1504 urteen artean egindako David, 5,17 metroko eskultura ikusgarria. Obra hori zizelkatzeko, Michelangelo Carrarako harrobietako marmol-bloke trinko batetik abiatu zen. Urteak pasatu diren arren, formula bera erabiltzen da oraindik egungo fabrikazio-teknologia erabilienean, mekanizazioan. Gauza batzuek bere horretan diraute.
Dena den, fabrikazio-teknologiek XVIII. mendearen bukaeratik aurrera izan dute garapenik handiena, industria-iraultzek ekarritako aurrerapenei esker. XXI. mendeko fabrikazioan, makinek eta automatizazioak hartu dute Michelangeloren eskuen lekua. Gaur egun, 4.0 Industriaren aroan gaudela esan ohi da. Ekoizpen-sistema adimendunak eta informazio-teknologiak industria-sistemetan integratzen dira, eta integrazio ziberfisiko horrek eraginkortasun handiko fabrika adimendunak sortzen ditu, zeinak kalitate handiko produktuak fabrikatzeko gai baitira.
Paradigma-aldaketa
Michelangelok eta Paleolitoko lehen gizaki haiek egin bezala, mekanizazioaren bidez piezak fabrikatzeko prozesua bloke batetik abiatzen da, eta, horri materiala kenduz, piezaren azken forma lortzen da. Fabrikazio gehigarrian, aldiz, fabrikazio-paradigma aldatzen da: hiru dimentsioko (3D) diseinu digital batetik abiatuta, geruzaz geruza materiala gehitzen da, eta, hala, objektu fisiko bat fabrikatzen da (2. irudia).
Fabrikazio gehigarria 1986an erabili zen lehen aldiz, estereolitografia sortu zenean; teknologia horrek izpi ultramoreak erabiltzen ditu polimero fotosentikorrak geruzaz geruza sortzeko. Jatorrian, fabrikazio gehigarriari 3D inprimaketa ere deitu zitzaion, eta, hasiera batean, prototipo azkarrak egiteko garatu zen. Azken urteetan, ordea, handitu egin dira fabrikazio gehigarriko tekniken zehaztasuna, errepikakortasuna eta fidagarritasuna, eta orain fabrikazio gehigarriko teknologia batzuk industria-ekoizpenerako bideragarritzat jotzen dira. Gaur egun, fabrikazio gehigarriak trinkotasun handiko piezak sor ditzake material-sorta zabal batean, hala nola polimeroetan, metaletan, material zeramikoetan, konpositeetan eta abarretan.
Horrelako teknologiak disruptiboak izango direla aurreikusten da; munduko ekoizpen-sarea eraldatuko dute, eta ezinbesteko tresna bilakatuko dira hainbat industria-sektoretarako. Izan ere, fabrikazio gehigarriak 4.0 Industriak planteatzen duen ekoizpen-sistemaren garapenari erantzuten dio, hasierako diseinutik azken piezarako bidea errazten baitu.
Zergatik gehitu?
Fabrikazio gehigarriaren abantaila nagusietako bat zera da, konplexutasun geometriko handiko piezak fabrikatzeko gaitasuna. Beste teknologia batzuk erabilita, ezinezkoa litzateke era horretako piezak egitea; esaterako, pieza hutsak, xehetasun konplexukoak edo barne-saredunak. Fabrikazio gehigarriaren bidez, askatasun handia lortzen da diseinuan, eta hori funtsezkoa da pisu txikia eskatzen duten aplikazioetarako, edo teknika tradizionalekin fabrikatuz gero osagai asko izango lituzketen piezak osagai bakarrekoak izan daitezen. Hona adibide ezagun bat: General Electric konpainiak fabrikazio gehigarriaren bidez sortutako erregai-injektoreak jarri zituen bere CFM LEAP hegazkin-motorrean; injektore berriak bloke bakarrean fabrikatuta zeuden, eta hasierako hemezortzi osagaiko sistema baino % 25 arinagoak ziren.
Gainera, fabrikazio gehigarriak azken produktua pertsonalizatzeko aukera ematen du. Aukera hori mugatua da fabrikazio-teknika tradizionaletan, dakarren kostuagatik. Izan ere, piezak ekoizteko erabiltzen diren moldeak eta tresneriaren diseinua aldatu behar izaten dira, eta horren kostua ez da bideragarria izaten. Aldiz, fabrikazio gehigarriaren bidez, piezak diseinatu eta zuzenean fabrikatzen direnez, bideragarria da pieza bakarrak eta pertsonalizatuak egitea.
Bestalde, fabrikazio gehigarriko teknologien bidez, amaierako geometriatik hurbil dauden piezak lortzen dira, materiala benetan beharrezkoa den tokian soilik ezartzen delako. Hala, lehengaien aprobetxamendu-tasa oso handia da (ikus 2. irudia). Hori dela eta, fabrikazio gehigarria aukera lehiakor bat izan daiteke erabilitako materialak (titanioa, nikel-aleazioak, etab.) garestiak direnean; esate baterako, industria aeronautikoan.
Azkenik, fabrikazio gehigarriko teknologiek erakutsi dute oso egokiak direla energia-kontsumoa txikitzeko, material gutxiago alferrik galtzeko eta mekanizazio-urratsak ezabatzeko edo murrizteko. Esaterako, zenbait azterketatan ikusi denez, fabrikazio gehigarriaren erabilera orokortuak % 27 jaitsiko luke energia-eskaria.
Metalak metatzen
Fabrikazio gehigarriaren barruan, teknologia-mota bakoitza energia-iturri baten, erabili beharreko materialaren formatuaren eta sistema mugikor baten konbinazio berezi bat da, eta konbinazio bakoitzak aplikazio jakin baterako balio du. ASTM elkarteak (Proba eta Materialetarako Estatu Batuetako Elkartea) sortutako terminologia estandarraren arabera, fabrikazio gehigarriko teknologiak zazpi kategoriatan sailkatzen dira, eta horietatik lau material metalikoetan erabil daitezke, 3. irudian ikusten den bezala. Kategoria horietako bat zuzeneko energia jalkitze (directed energy deposition, DED) deritzona da. Hor biltzen diren teknika guztietan, materiala, elikatu ahala, energia-iturriaren bidez urtzen da. DED teknologian, materiala bi formatutan elika daiteke: hari gisa edo hauts gisa. Hautsaren ordez haria erabiltzeak baditu zenbait abantaila: prezioa murrizten du, materialaren erabileraren eraginkortasuna handitzen du eta laneko segurtasun- eta osasun-arriskuak minimizatzen ditu. Materiala urtzeko energia-iturri gisa, berriz, laser bat, elektroi-sorta bat edo arku elektriko bat erabil daitezke. Zehazki, nire tesian aztertu dudan hari eta arku bidezko fabrikazio gehigarriko prozesuan (wire arc additive manufacturing, WAAM) materiala hari gisa elikatzen da, eta arku elektriko baten bidez urtzen.
Gaur egun, WAAM teknologia fabrikazio-prozesu interesgarri bihurtu da, tamaina handiko eta konplexutasun geometriko ertaineko pieza metalikoak kostu txikian fabrikatzeko aukera ematen duelako. Ezaugarriei dagokienez, WAAM teknologia soldadura automatikoko prozesu baten antzekoa da: energia-iturriak haria urtzen du arku elektriko baten bidez, eta, manipulazio-sistemaren bidez, metal urtua oinarri-materialaren gainean ezartzen du geruzaz geruza, helburuko geometria osatu arte.
Haria eta arkua
Erabilitako soldadura-iturriaren arabera, WAAM prozesu-mota desberdinak daude. Hain zuzen ere, nik gasez babestutako arku metalikozko soldadura (gas metal arc welding, GMAW) teknologian oinarritutako WAAM prozesua landu dut, interesgarria izan baitaiteke industrian erabiltzeko, lortzen dituen produktibitate-tasa handiak (1-10 kg/h) direla eta.
GMAW teknologian (ikus 3. irudiaren eskuinaldea) haria da elektrodo kontsumigarria. Alegia, materiala jartzeko, intentsitate-seinale bat ezartzen da harian, eta arku elektriko bat eratzen da hariaren eta piezaren artean. Arku elektriko horri esker, metala urtu egiten da, eta metal-tantak haritik piezara transferitzen dira. 4. irudian, metal urtuaren tantak sortzeko prozesuaren eta intentsitate-seinalearen arteko korrelazioa ikus daiteke.
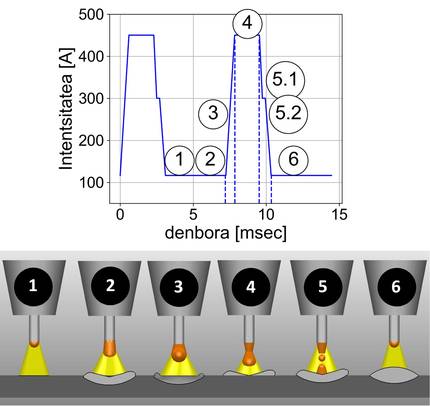
Transferentzia hori hainbat modutan gerta daiteke: esprai gisa, era globularrean edo zirkuitu labur bidez. Azken hamarkadetan, maiztasun handiko kontrol-estrategiak dituzten soldadura-iturriak erabiltzen dira materialaren transferentzia kontrolatzeko. Kontrol-estrategia horiek hariari aplikatutako intentsitate-seinalearen forma (uhin-forma, maiztasuna, etab.) definitzen dute. Nik altzairu- eta aluminio-aleazioetarako dauden transferentzia-moduak aztertu ditut tesian; ikusi dudanez, transferentzia-moduek eragin nabarmena dute piezari egiten zaion bero-ekarpenenean, eta horrek baldintzatu egiten ditu bai ezarpenaren geometria, bai produktibitatea. Horrez gain, transferentzia-moduek aluminioan lortzen den porositate-mailan duten eragina ere aztertu dut.
Amaitzeko, 5. irudian GMAW teknologian oinarritutako WAAM prozesuaren bidez hasierako diseinutik abiatuta piezak fabrikatzeko jarraitu beharreko bidea azaltzen da. Behin diseinua definituta dagoenean, pieza geruzatan banatzen da, eta geruza bakoitzaren ezarpen-ibilbideak sortzen dira. Ondoren, prozesuaren parametroak zehazten dira, eta pieza robot baten edo CNC makina baten bidez fabrikatzen da. Fabrikatu bitartean, prozesuaren barne-parametroak monitorizatzen dira, baita makinan instalatutako sentsoreenak ere. Prozesua denbora errealean monitorizatutako datuen bidez kontrolatzen da, eta, azkenik, lortutako pieza neurtzen da, perdoiaren barruan dagoela ziurtatzeko.
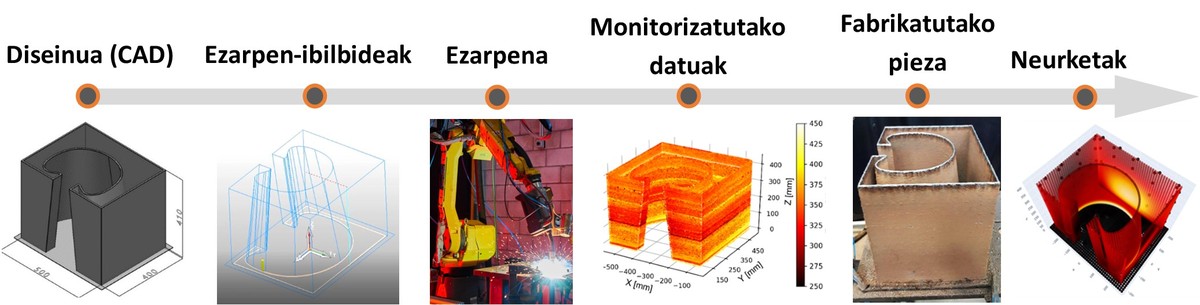
Nire tesiaren helburu nagusia oinarriak ezartzea izan da, makinek ahalik eta modu autonomoenean egin dezaten hasierako diseinutik bukaerako piezara arteko ibilbidea. Botoi bati eman, eta, Michelangeloren eskuak bailiran, robota bere kasa piezak fabrikatzen has dadila.
Bibliografia
Aldalur, E., Suárez, A., & Veiga, F. 2021. “Influence of Wire Arc Additive Manufacturing metal transfer modes on droplet formation, heat input, microstructure and porosity of as-built Al-Mg alloys”. Journal of Material Processing Technology, 2021, 297, 117271.
Cunningham, C. R., Flynn, J. M., Shokrani, A., Dhokia, V., & Newman, S. T. 2018. “Invited review article: Strategies and processes for high quality wire arc additive manufacturing”. Additive Manufacturing, 22, 672–686.
Dilberoglu, U. M., Gharehpapagh, B., Yaman, U., Dolen, M. 2017. “The Role of Additive Manufacturing in the Era of Industry 4.0”. Procedia Manufacturing, 11, 545–554.
General Electric. 2017. “GE Global Research, 3D Printing New Parts for Aircraft Engines”.
Herzog, D., Seyda, V., Wycisk, E., & Emmelmann, C. 2016. “Additive manufacturing of metals”. Acta Materialia, 117, 371–392.
ISO/ASTM. ISO/ASTM 52900. 2015. Additive manufacturing - General principles - Terminology. International Standard, 5, 1–26.
Suárez, A., Aldalur, E., Veiga, F., Artaza, T., Tabernero, I., & Lamikiz, A. 2021. “Wire arc additive manufacturing of an aeronautic fitting with different metal alloys: From the design to the part”. Journal of Manufacturing Processes, 64, 188–197.
Sun, C., Wang, Y., McMurtrey, M. D., Jerred, N. D., Liou, F., & Li, J. 2021. “Additive manufacturing for energy: A review”. Applied Energy, 282.
Williams, S. W., Martina, F., Addison, A. C., Ding, J., Pardal, G., & Colegrove, P. 2016. “Wire + Arc additive manufacturing”. Materials Science and Technology, 32(7), 641–647.
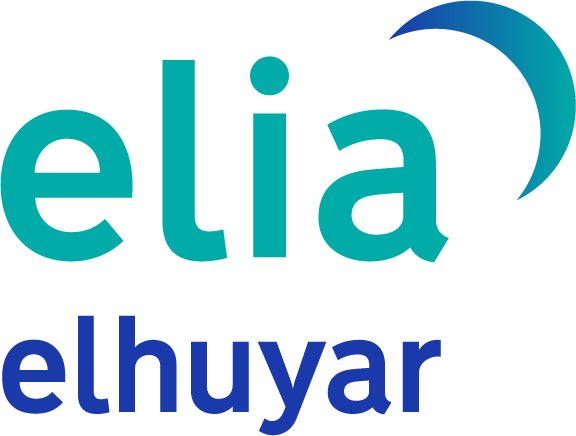