De llevar a afegir: apilant metalls
2025/03/01 Aldalur Urresti, Eider - Tecnaliako ikertzailea, Ingeniaritza Mekanikoan doktorea Iturria: Elhuyar aldizkaria
Al llarg de la història, les tecnologies de fabricació i la indústria en general han anat evolucionant fins a arribar a les tecnologies de fosa, conformat i mecanitzat que són avui dia els pilars bàsics de la indústria dels metalls a nivell mundial. Els avanços tecnològics dels últims anys han fet necessari afegir a aquest llistat una innovadora tecnologia de fabricació: la fabricació additiva.
Les petjades dels primers instruments de pedra creats per l'home ens retrotreuen a 3,4 milions d'anys, a l'Edat de Pedra. En aquella època, l'home va començar per primera vegada a treballar pedres, colpejant-se els uns contra els altres per a fabricar eines, armes i puntes d'aresta esmolada mitjançant l'extracció. D'aquesta manera, es va establir el primer precedent de les tecnologies actuals de mecanitzat. A continuació, en el Neolític, es va deixar d'utilitzar la pedra com a element bàsic per a la fabricació d'artefactes i es va començar a treballar en els metalls, primer mitjançant el martellejo en fred (precursor de la conformació actual) i, posteriorment, mitjançant la fosa de minerals (precursor de la fosa moderna).
Des que l'home va col·locar la primera pedra del mecanitzat modern en el Paleolític, aquestes tecnologies de fabricació han tingut un gran desenvolupament, com s'observa en la figura 1. Prova d'això és, per exemple, la impressionant escultura de 5,17 metres realitzada pel gran escultor i pintor italià Michelangelo Buonarroti entre 1501 i 1504. Per a tallar aquesta obra, Miguel Ángel va partir d'un dens bloc de marbre de les pedreres de Carrara. Malgrat els anys, la fórmula continua sent la mateixa en la tecnologia de fabricació més utilitzada en l'actualitat, en el mecanitzat. Hi ha coses que romanen inalterables.
No obstant això, les tecnologies de fabricació han estat les que han experimentat un major desenvolupament a partir de finals del segle XVIII, gràcies als avanços de les revolucions industrials. En la fabricació del segle XXI, les mans de Miguel Ángel han estat substituïdes per les màquines i l'automatització. Avui dia, es diu que estem en l'era de la Indústria 4.0. Els sistemes de producció intel·ligents i les tecnologies de la informació s'integren en els sistemes industrials, i aquesta integració ciber-física genera fàbriques intel·ligents i d'alta eficiència que són capaces de fabricar productes d'alta qualitat.
Canvi de paradigma
Igual que Miguel Ángel i aquells primers éssers humans del Paleolític, el procés de fabricació de peces per mecanitzat part d'un bloc, al qual se li lleva el material s'obté la forma final de la peça. En la fabricació additiva, per contra, es modifica el paradigma de fabricació: a partir d'un disseny digital tridimensional (3D), s'afegeix capa a capa a capa material, fabricant un objecte físic (Figura 2).
La fabricació additiva es va utilitzar per primera vegada en 1986, quan es va crear l'estereolitografia, tecnologia que utilitza els raigs ultraviolats per a formar els polímers fotosensibles per capes. Originalment, la fabricació additiva també es va denominar impressió 3D i es va desenvolupar inicialment per a la fabricació de prototips ràpids. No obstant això, en els últims anys s'ha produït un increment en la precisió, repetitividad i fiabilitat de les tècniques de fabricació additiva, i ara algunes tecnologies de fabricació additiva es consideren viables per a la producció industrial. Actualment, la fabricació additiva pot produir peces d'alta consistència en una àmplia gamma de materials com a polímers, metalls, materials ceràmics, compòsits, etc.
Aquest tipus de tecnologies es preveu disruptives que transformaran el teixit productiu mundial i es convertiran en una eina imprescindible per als diferents sectors industrials. De fet, la fabricació additiva respon al desenvolupament del sistema productiu que planteja la Indústria 4.0, ja que facilita el trànsit des del disseny inicial fins a la peça final.
Per què afegir-ho?
Una dels principals avantatges de la fabricació additiva és la capacitat de fabricar peces d'alta complexitat geomètrica. La utilització d'altres tecnologies faria impossible aquest tipus de peces, com a peces buides, amb detalls complexos o amb xarxes internes. La fabricació additiva permet una gran llibertat en el disseny, la qual cosa resulta fonamental per a aplicacions que requereixen poc pes, o perquè peces que, si es fabriquen amb tècniques tradicionals, tindrien molts components siguin d'un sol component. Un exemple conegut és: La companyia General Electric va instal·lar en el seu motor d'aviació CFM LEAP injectors de combustible procedents de fabricació additiva, fabricats en un únic bloc, un 25% més lleugers que el sistema de divuit components inicials.
A més, la fabricació additiva permet personalitzar el producte final. Aquesta opció és limitada en les tècniques tradicionals de fabricació pel cost que suposa. De fet, els motlles que s'utilitzen per a la producció de peces i el disseny dels utillatges han de ser modificats i el seu cost no és viable.Per contra, la fabricació additiva permet dissenyar i fabricar peces de manera directa, per la qual cosa és factible fabricar peces úniques i personalitzades.
D'altra banda, mitjançant tecnologies de fabricació additiva s'obtenen peces pròximes a la geometria final, ja que el material s'implanta només on realment és necessari. Així, la taxa d'aprofitament de matèries primeres és molt elevada (veure figura 2). Per això, la fabricació additiva pot ser una opció competitiva per als materials emprats (titani, aliatges de níquel, etc.). quan són cars, per exemple en la indústria aeronàutica.
Finalment, les tecnologies de fabricació additiva han demostrat ser molt adequades per a reduir el consum d'energia, reduir el desaprofitament de materials i eliminar o reduir els passos de mecanitzat. Per exemple, en alguns estudis s'observa que l'ús generalitzat de la fabricació additiva reduiria en un 27% la demanda d'energia.
Acumulant metalls
Dins de la fabricació additiva, cada tipus de tecnologia és una combinació especial d'una font d'energia, el format del material a utilitzar i un sistema mòbil, i cada combinació serveix per a una aplicació concreta. Segons la terminologia estàndard creada per l'associació ASTM (Associació de Proves i Materials dels Estats Units), les tecnologies de fabricació additiva es classifiquen en set categories, de les quals quatre poden ser utilitzades en materials metàl·lics, tal com es mostra en la figura 3. Una d'aquestes categories és la denominada deposició d'energia directa (directed energy deposition, DED). En totes les tècniques que es recullen, el material es fundi a mesura que es va alimentant a través de la font d'energia. En tecnologia DED, el material pot ser alimentat en dos formats: fils o pols. L'ús de la línia en lloc de pols presenta avantatges quant a reducció de preu, augment de l'eficiència en l'ús del material i minimització dels riscos per a la seguretat i la salut en el treball. Com a font d'energia per a fondre el material, es pot utilitzar un làser, un feix d'electrons o un arc elèctric. En concret, en el procés de fabricació additiva per fil i arc que he analitzat en la meva tesi (wire arc additive manufacturing, WAAM) el material s'alimenta com a fil i es fundi amb un arc elèctric.
En l'actualitat, la tecnologia WAAM s'ha convertit en un interessant procés de fabricació, ja que permet fabricar peces metàl·liques de gran grandària i de mitjana complexitat geomètrica a baix cost. Quant a les característiques, la tecnologia WAAM és similar a un procés de soldadura automàtica: la font d'energia fundi el fil mitjançant un arc elèctric i, mitjançant el sistema de manipulació, col·loca el metall fos sobre el material base capa a capa fins a completar la geometria del destí.
Fil i arc
Existeixen diferents tipus de processos WAAM en funció de la font de soldadura utilitzada. De fet, jo he treballat en el procés WAAM basat en la tecnologia de soldadura per arc metàl·lic protegida per gas (gas metall arc welding, GMAW), que pot ser d'interès per al seu ús en la indústria a causa de les altes taxes de productivitat que aconsegueix (1-10 kg/h).
En tecnologia GMAW (veure figura 3 dreta) el cable és l'elèctrode consumible. És a dir, per a la col·locació del material s'estableix un senyal d'intensitat en el fil i es forma un arc elèctric entre el fil i la peça. Aquest arc elèctric permet fondre el metall i transferir les gotes de metall del fil a la peça. La figura 4 mostra la correlació entre el procés de generació de les gotes del metall fos i el senyal d'intensitat.
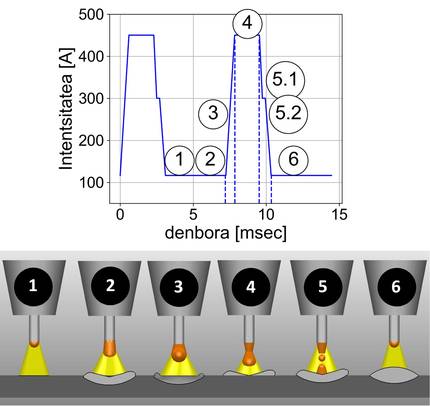
Aquesta transferència pot produir-se en forma d'esprai, de manera globular o per circuits curts. En les últimes dècades s'han utilitzat fonts de soldadura amb estratègies de control d'alta freqüència per a controlar la transferència de material. La forma del senyal d'intensitat aplicada al fil per aquestes estratègies de control (forma d'ona, freqüència, etc.) defineixen. En la meva tesi he analitzat les diferents formes de transferència per als aliatges d'acer i alumini, observant que les formes de transferència exerceixen una influència notable en l'aportació de calor a la peça, la qual cosa condiciona tant la geometria de la implantació com la productivitat. També he analitzat la influència dels modes de transferència en el grau de porositat que s'aconsegueix en l'alumini.
Finalment, la figura 5 mostra el camí a seguir per a la fabricació de peces a partir del disseny inicial a través del procés WAAM basat en tecnologia GMAW. Una vegada definit el disseny, la peça es divideix en capes i es creen les trajectòries d'implantació de cada capa. A continuació es defineixen els paràmetres del procés i la peça es fabrica mitjançant un robot o màquina CNC. Durant la fabricació es monitoren els paràmetres interns del procés així com els dels sensors instal·lats en la màquina. El procés es controla mitjançant dades monitorades en temps real i, finalment, es mesura la peça obtinguda per a assegurar que es troba dins de la tolerància.
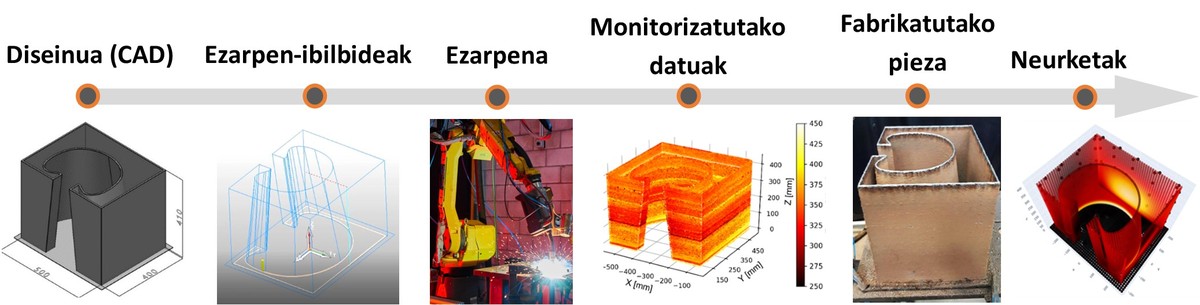
L'objectiu principal de la meva tesi ha estat establir les bases perquè les màquines puguin recórrer de la forma més autònoma possible el recorregut des del disseny inicial fins a la peça final. Dona-li a un botó i que, com les mans de Miguel Ángel, el robot es posi a fabricar peces pel seu compte.
Bibliografia
Aldalur, E., Suárez, A., & Veiga, F. 2021. “Influence of Wire Arc Additive Manufacturing metall transfer modes on droplet formation, heat input, microstructure and porosity of as-built Al-Mg alloys”. Journal of material Processing Technology, 2021, 297, 117271.
Cunningham, C. R., Flynn, J. M., Shokrani, A. Dhokia, V. & Newman, S. T. 2018. “Invited review article: Strategies and processes for high quality wire arc additive manufacturing”. Additive Manufacturing, 22, 672–686.
Dilberoglu, O. M., Gharehpapagh, B. Yaman, O. Dolen, M. 2017. “The Role of Additive Manufacturing in the Era of Industry 4.0”. Procedia Manufacturing, 11, 545–554.
General Electric. 2017. “GE Global Research, 3D Printing New Parts for Aircraft Engines”.
Herzog, D., Seyda, V. Wycisk, E. & Emmelmann, C. 2016. Additive manufacturing of metals. Acta Materialia, 117, 371–392.
ISO/ASTM. ISO/ASTM 52900. 2015. Additive manufacturing - General principles - Terminology. International Standard, 5, 1–26.
Suárez, A., Aldalur, E., Veiga, F., Artaza, T., Tabernero, I., & Lamikiz, A. 2021. “Wire arc additive manufacturing of an aeronáutic fitting with different metall alloys: From the design to the part”. Journal of Manufacturing Processes, 64, 188–197.
Sun, C., Wang, I., Murtrey, M. D., Jerred, N. D., Liou, F. & Li, J. 2021. “Additive manufacturing for energy: A review”. Applied Energy 282.
Williams, S. W. Martina, F., Addison, A. C., Ding, J. Pardal, G., & Colegrove, P. 2016. “Wire + Arc additive manufacturing”. Materials Science and Technology, 32(7), 641–647.
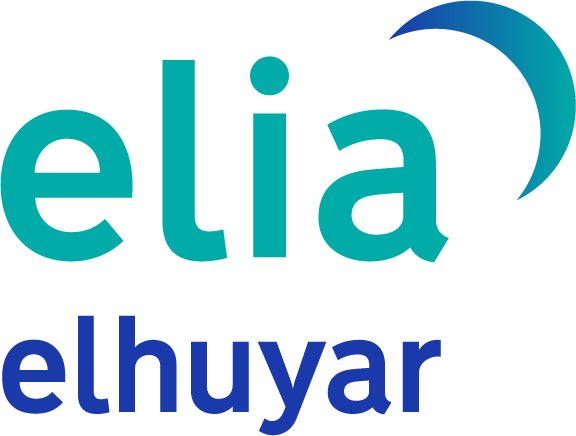