De quitar a añadir: apilando metales
2025/03/01 Aldalur Urresti, Eider - Tecnaliako ikertzailea, Ingeniaritza Mekanikoan doktorea Iturria: Elhuyar aldizkaria
A lo largo de la historia, las tecnologías de fabricación y la industria en general han ido evolucionando hasta llegar a las tecnologías de fundición, conformado y mecanizado que son hoy en día los pilares básicos de la industria de los metales a nivel mundial. Los avances tecnológicos de los últimos años han hecho necesario añadir a este listado una innovadora tecnología de fabricación: la fabricación aditiva.
Las huellas de los primeros instrumentos de piedra creados por el hombre nos retrotraen a 3,4 millones de años, a la Edad de Piedra. En aquella época, el hombre comenzó por primera vez a trabajar piedras, golpeándose unos contra otros para fabricar herramientas, armas y puntas de arista afilada mediante la extracción. De este modo, se estableció el primer precedente de las tecnologías actuales de mecanizado. A continuación, en el Neolítico, se dejó de utilizar la piedra como elemento básico para la fabricación de artefactos y se comenzó a trabajar en los metales, primero mediante el martilleo en frío (precursor de la conformación actual) y, posteriormente, mediante la fundición de minerales (precursor de la fundición moderna).
Desde que el hombre colocó la primera piedra del mecanizado moderno en el Paleolítico, estas tecnologías de fabricación han tenido un gran desarrollo, como se observa en la figura 1. Prueba de ello es, por ejemplo, la impresionante escultura de 5,17 metros realizada por el gran escultor y pintor italiano Michelangelo Buonarroti entre 1501 y 1504. Para tallar esta obra, Miguel Ángel partió de un denso bloque de mármol de las canteras de Carrara. A pesar de los años, la fórmula sigue siendo la misma en la tecnología de fabricación más utilizada en la actualidad, en el mecanizado. Hay cosas que permanecen inalterables.
Sin embargo, las tecnologías de fabricación han sido las que han experimentado un mayor desarrollo a partir de finales del siglo XVIII, gracias a los avances de las revoluciones industriales. En la fabricación del siglo XXI, las manos de Miguel Ángel han sido sustituidas por las máquinas y la automatización. Hoy en día, se dice que estamos en la era de la Industria 4.0. Los sistemas de producción inteligentes y las tecnologías de la información se integran en los sistemas industriales, y esta integración ciber-física genera fábricas inteligentes y de alta eficiencia que son capaces de fabricar productos de alta calidad.
Cambio de paradigma
Al igual que Miguel Ángel y aquellos primeros seres humanos del Paleolítico, el proceso de fabricación de piezas por mecanizado parte de un bloque, al que se le quita el material se obtiene la forma final de la pieza. En la fabricación aditiva, por el contrario, se modifica el paradigma de fabricación: a partir de un diseño digital tridimensional (3D), se añade capa a capa a capa material, fabricando un objeto físico (Figura 2).
La fabricación aditiva se utilizó por primera vez en 1986, cuando se creó la estereolitografía, tecnología que utiliza los rayos ultravioleta para formar los polímeros fotosensibles por capas. Originalmente, la fabricación aditiva también se denominó impresión 3D y se desarrolló inicialmente para la fabricación de prototipos rápidos. Sin embargo, en los últimos años se ha producido un incremento en la precisión, repetitividad y fiabilidad de las técnicas de fabricación aditiva, y ahora algunas tecnologías de fabricación aditiva se consideran viables para la producción industrial. Actualmente, la fabricación aditiva puede producir piezas de alta consistencia en una amplia gama de materiales como polímeros, metales, materiales cerámicos, composites, etc.
Este tipo de tecnologías se prevé disruptivas que transformarán el tejido productivo mundial y se convertirán en una herramienta imprescindible para los diferentes sectores industriales. De hecho, la fabricación aditiva responde al desarrollo del sistema productivo que plantea la Industria 4.0, ya que facilita el tránsito desde el diseño inicial hasta la pieza final.
¿Por qué añadirlo?
Una de las principales ventajas de la fabricación aditiva es la capacidad de fabricar piezas de alta complejidad geométrica. La utilización de otras tecnologías haría imposible este tipo de piezas, como piezas vacías, con detalles complejos o con redes internas. La fabricación aditiva permite una gran libertad en el diseño, lo que resulta fundamental para aplicaciones que requieren poco peso, o para que piezas que, si se fabrican con técnicas tradicionales, tendrían muchos componentes sean de un solo componente. Un ejemplo conocido es: La compañía General Electric instaló en su motor de aviación CFM LEAP inyectores de combustible procedentes de fabricación aditiva, fabricados en un único bloque, un 25% más ligeros que el sistema de dieciocho componentes iniciales.
Además, la fabricación aditiva permite personalizar el producto final. Esta opción es limitada en las técnicas tradicionales de fabricación por el coste que supone. De hecho, los moldes que se utilizan para la producción de piezas y el diseño de los utillajes tienen que ser modificados y su coste no es viable.Por el contrario, la fabricación aditiva permite diseñar y fabricar piezas de forma directa, por lo que es factible fabricar piezas únicas y personalizadas.
Por otra parte, mediante tecnologías de fabricación aditiva se obtienen piezas cercanas a la geometría final, ya que el material se implanta sólo donde realmente es necesario. Así, la tasa de aprovechamiento de materias primas es muy elevada (ver figura 2). Por ello, la fabricación aditiva puede ser una opción competitiva para los materiales empleados (titanio, aleaciones de níquel, etc.). cuando son caros, por ejemplo en la industria aeronáutica.
Por último, las tecnologías de fabricación aditiva han demostrado ser muy adecuadas para reducir el consumo de energía, reducir el desperdicio de materiales y eliminar o reducir los pasos de mecanizado. Por ejemplo, en algunos estudios se observa que el uso generalizado de la fabricación aditiva reduciría en un 27% la demanda de energía.
Acumulando metales
Dentro de la fabricación aditiva, cada tipo de tecnología es una combinación especial de una fuente de energía, el formato del material a utilizar y un sistema móvil, y cada combinación sirve para una aplicación concreta. Según la terminología estándar creada por la asociación ASTM (Asociación de Pruebas y Materiales de Estados Unidos), las tecnologías de fabricación aditiva se clasifican en siete categorías, de las cuales cuatro pueden ser utilizadas en materiales metálicos, tal y como se muestra en la figura 3. Una de estas categorías es la denominada deposición de energía directa (directed energy deposition, DED). En todas las técnicas que se recogen, el material se funde a medida que se va alimentando a través de la fuente de energía. En tecnología DED, el material puede ser alimentado en dos formatos: hilos o polvo. El empleo de la línea en lugar de polvo presenta ventajas en cuanto a reducción de precio, aumento de la eficiencia en el uso del material y minimización de los riesgos para la seguridad y la salud en el trabajo. Como fuente de energía para fundir el material, se puede utilizar un láser, un haz de electrones o un arco eléctrico. En concreto, en el proceso de fabricación aditiva por hilo y arco que he analizado en mi tesis (wire arc additive manufacturing, WAAM) el material se alimenta como hilo y se funde con un arco eléctrico.
En la actualidad, la tecnología WAAM se ha convertido en un interesante proceso de fabricación, ya que permite fabricar piezas metálicas de gran tamaño y de mediana complejidad geométrica a bajo coste. En cuanto a las características, la tecnología WAAM es similar a un proceso de soldadura automática: la fuente de energía funde el hilo mediante un arco eléctrico y, mediante el sistema de manipulación, coloca el metal fundido sobre el material base capa a capa hasta completar la geometría del destino.
Hilo y arco
Existen diferentes tipos de procesos WAAM en función de la fuente de soldadura utilizada. De hecho, yo he trabajado en el proceso WAAM basado en la tecnología de soldadura por arco metálico protegida por gas (gas metal arc welding, GMAW), que puede ser de interés para su uso en la industria debido a las altas tasas de productividad que alcanza (1-10 kg/h).
En tecnología GMAW (ver figura 3 derecha) el cable es el electrodo consumible. Es decir, para la colocación del material se establece una señal de intensidad en el hilo y se forma un arco eléctrico entre el hilo y la pieza. Este arco eléctrico permite fundir el metal y transferir las gotas de metal del hilo a la pieza. La figura 4 muestra la correlación entre el proceso de generación de las gotas del metal fundido y la señal de intensidad.
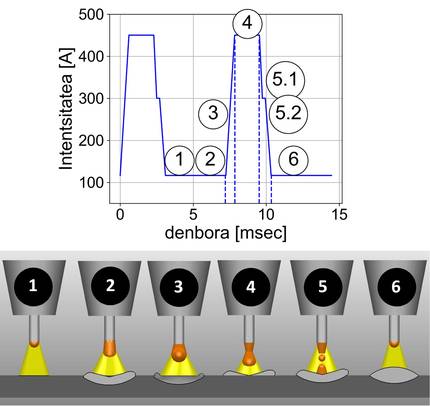
Esta transferencia puede producirse en forma de spray, de forma globular o por circuitos cortos. En las últimas décadas se han utilizado fuentes de soldadura con estrategias de control de alta frecuencia para controlar la transferencia de material. La forma de la señal de intensidad aplicada al hilo por estas estrategias de control (forma de onda, frecuencia, etc.) definen. En mi tesis he analizado las diferentes formas de transferencia para las aleaciones de acero y aluminio, observando que las formas de transferencia ejercen una influencia notable en la aportación de calor a la pieza, lo que condiciona tanto la geometría de la implantación como la productividad. También he analizado la influencia de los modos de transferencia en el grado de porosidad que se consigue en el aluminio.
Por último, la figura 5 muestra el camino a seguir para la fabricación de piezas a partir del diseño inicial a través del proceso WAAM basado en tecnología GMAW. Una vez definido el diseño, la pieza se divide en capas y se crean las trayectorias de implantación de cada capa. A continuación se definen los parámetros del proceso y la pieza se fabrica mediante un robot o máquina CNC. Durante la fabricación se monitorizan los parámetros internos del proceso así como los de los sensores instalados en la máquina. El proceso se controla mediante datos monitorizados en tiempo real y, finalmente, se mide la pieza obtenida para asegurar que se encuentra dentro de la tolerancia.
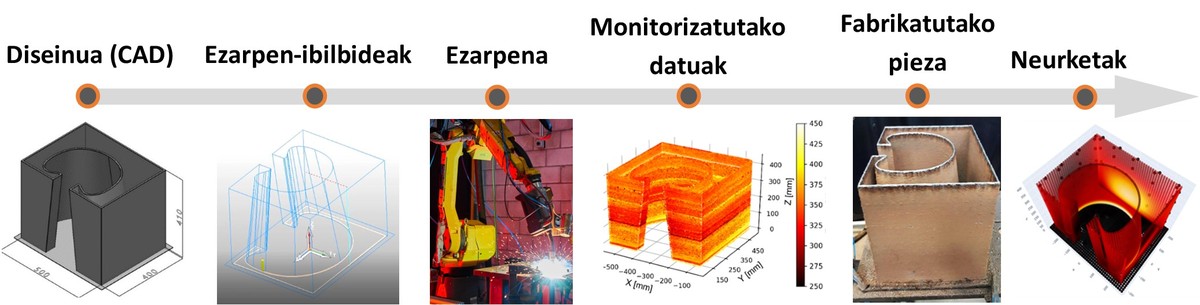
El objetivo principal de mi tesis ha sido sentar las bases para que las máquinas puedan recorrer de la forma más autónoma posible el recorrido desde el diseño inicial hasta la pieza final. Dale a un botón y que, como las manos de Miguel Ángel, el robot se ponga a fabricar piezas por su cuenta.
Bibliografía
Aldalur, E., Suárez, A., & Veiga, F. 2021. “Influence of Wire Arc Additive Manufacturing metal transfer modes on droplet formation, heat input, microstructure and porosity of as-built Al-Mg alloys”. Journal of material Processing Technology, 2021, 297, 117271.
Cunningham, C. R., Flynn, J. M., Shokrani, A. Dhokia, V. & Newman, S. T. 2018. “Invited review article: Strategies and processes for high quality wire arc additive manufacturing”. Additive Manufacturing, 22, 672–686.
Dilberoglu, U. M., Gharehpapagh, B. Yaman, U. Dolen, M. 2017. “The Role of Additive Manufacturing in the Era of Industry 4.0”. Procedia Manufacturing, 11, 545–554.
General Electric. 2017. “GE Global Research, 3D Printing New Parts for Aircraft Engines”.
Herzog, D., Seyda, V. Wycisk, E. & Emmelmann, C. 2016. Additive manufacturing of metals. Acta Materialia, 117, 371–392.
ISO/ASTM. ISO/ASTM 52900. 2015. Additive manufacturing - General principles - Terminology. International Standard, 5, 1–26.
Suárez, A., Aldalur, E., Veiga, F., Artaza, T., Tabernero, I., & Lamikiz, A. 2021. “Wire arc additive manufacturing of an aeronáutic fitting with different metal alloys: From the design to the part”. Journal of Manufacturing Processes, 64, 188–197.
Sun, C., Wang, Y., Murtrey, M. D., Jerred, N. D., Liou, F. & Li, J. 2021. “Additive manufacturing for energy: A review”. Applied Energy 282.
Williams, S. W. Martina, F., Addison, A. C., Ding, J. Pardal, G., & Colegrove, P. 2016. “Wire + Arc additive manufacturing”. Materials Science and Technology, 32(7), 641–647.
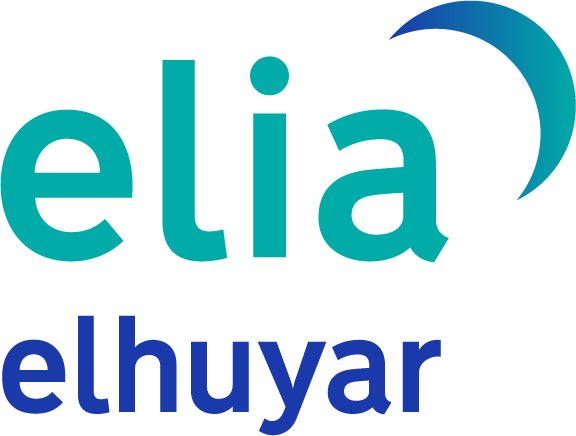