De l'élimination à l'addition: accumulation de métaux
2025/03/01 Aldalur Urresti, Eider - Tecnaliako ikertzailea, Ingeniaritza Mekanikoan doktorea Iturria: Elhuyar aldizkaria
Tout au long de l'histoire, les technologies de fabrication et l'industrie en général se sont développées pour atteindre les technologies de moulage, de formage et d'usinage qui sont aujourd'hui les principaux piliers de l'industrie des métaux dans le monde entier. Grâce aux avancées technologiques de ces dernières années, une technologie de fabrication innovante, la fabrication additive, doit être ajoutée à cette liste.
Les vestiges des premiers outils en pierre créés par l’homme remontent à 3,4 millions d’années, à l’âge de pierre. C'est à cette époque que l'homme commença pour la première fois à travailler des pierres en les frappant les unes contre les autres pour fabriquer des outils, des armes et des pointes à bord tranchant par extraction. C'est ainsi qu'a été établi le premier précédent des technologies d'usinage actuelles. Ensuite, au Néolithique, la pierre a cessé d'être utilisée comme élément de base pour la fabrication d'artefacts et a commencé à travailler les métaux, d'abord par le martelage à froid (précurseur de la conformation actuelle), puis par la fonte des minéraux (précurseur de la fonte moderne).
Depuis que l'homme a posé la première pierre de l'usinage moderne dans le paléolithique, ces technologies de fabrication ont connu un grand développement, comme le montre la figure 1. Le David, réalisé entre 1501 et 1504 par le grand sculpteur et peintre italien de la Renaissance Michelangelo Buonarroti, est un exemple de ce chemin, une sculpture impressionnante de 5,17 mètres. Pour sculpter cette œuvre, Michel-Ange partit d’un bloc de marbre massif des carrières de Carrare. Bien que des années se soient écoulées, la même formule est toujours utilisée dans la technologie de fabrication la plus utilisée aujourd'hui, l'usinage. Certaines choses restent intactes.
Cependant, les technologies de fabrication ont connu leur plus grand développement à partir de la fin du XVIIIe siècle, grâce aux progrès apportés par les révolutions industrielles. Dans la fabrication du XXIe siècle, les machines et l’automatisation ont pris la place des mains de Michel-Ange. Aujourd'hui, on dit que nous sommes à l'ère de l'Industrie 4.0. Les systèmes de production intelligents et les technologies de l'information s'intègrent dans les systèmes industriels, et cette intégration cyberphysique crée des usines intelligentes à haute efficacité, capables de fabriquer des produits de haute qualité.
Changement de paradigme
Comme l'ont fait Michel-Ange et les premiers humains du Paléolithique, le processus de fabrication des pièces par usinage commence à partir d'un bloc, à partir duquel le matériau est enlevé, on obtient la forme finale de la pièce. Dans la fabrication additive, en revanche, le paradigme de fabrication change: à partir d'une conception numérique tridimensionnelle (3D), le matériau est ajouté couche par couche, de sorte qu'un objet physique est fabriqué (figure 2).
La fabrication additive a été utilisée pour la première fois en 1986 avec la création de la stéréolithographie, une technologie qui utilise des rayons ultraviolets pour produire des polymères photosensibles couche par couche. À l'origine, la fabrication additive a également été appelée impression 3D et a été initialement développée pour la réalisation de prototypes rapides. Cependant, au cours des dernières années, la précision, la répétabilité et la fiabilité des techniques de fabrication additive ont augmenté et certaines technologies de fabrication additive sont maintenant considérées comme viables pour la production industrielle. Aujourd'hui, la fabrication additive peut produire des pièces de haute consistance dans une large gamme de matériaux tels que les polymères, les métaux, les matériaux céramiques, les composites, etc.
Ces technologies devraient être disruptives, transformer le réseau mondial de production et devenir un outil indispensable pour divers secteurs industriels. En effet, la fabrication additive répond au développement du système de production posé par l’Industrie 4.0, qui ouvre la voie de la conception initiale à la pièce finale.
Pourquoi l'ajouter ?
L'un des principaux avantages de la fabrication additive est sa capacité à fabriquer des pièces d'une grande complexité géométrique. L'utilisation d'autres technologies rendrait impossible la fabrication de pièces de ce type, telles que des pièces creuses, des détails complexes ou des grilles internes. Grâce à la fabrication additive, une grande liberté de conception est obtenue, ce qui est essentiel pour les applications nécessitant peu de poids, ou pour que les pièces qui auraient de nombreux composants si elles étaient fabriquées avec des techniques traditionnelles soient composées d'un seul composant. Voici un exemple bien connu: La société General Electric a installé des injecteurs de carburant générés par la fabrication additive sur son moteur d'avion CFM LEAP; les nouveaux injecteurs étaient fabriqués en un seul bloc et étaient 25 % plus légers que le système initial de dix-huit composants.
De plus, la fabrication additive permet de personnaliser le produit final. Cette option est limitée dans les techniques de fabrication traditionnelles en raison du coût qu'elle implique. En effet, il est souvent nécessaire de modifier les moules et la conception de l'outillage utilisés pour la production des pièces, dont le coût n'est généralement pas viable.En revanche, grâce à la fabrication additive, les pièces étant conçues et fabriquées directement, il est possible de fabriquer des pièces uniques et personnalisées.
D'autre part, les technologies de fabrication additive permettent d'obtenir des pièces proches de la géométrie finale, car le matériau n'est implanté que là où il est vraiment nécessaire. Ainsi, le taux d'utilisation des matières premières est très élevé (voir figure 2). Pour cette raison, la fabrication additive peut être un choix concurrentiel des matériaux utilisés (titane, alliages de nickel, etc.) lorsqu'elles sont coûteuses, par exemple dans l'industrie aéronautique.
Enfin, les technologies de fabrication additive se sont avérées idéales pour réduire la consommation d'énergie, réduire le gaspillage de matériaux et éliminer ou réduire les étapes d'usinage. Par exemple, plusieurs études ont montré que l'utilisation généralisée de la fabrication additive réduirait la demande d'énergie de 27 %.
Accumulation des métaux
Dans le cadre de la fabrication additive, chaque type de technologie est une combinaison spéciale d'une source d'énergie, du format du matériau à utiliser et d'un système mobile, chaque combinaison étant valable pour une application spécifique. Selon la terminologie standard créée par l’association ASTM (American Association for Testing and Materials), les technologies de fabrication additive sont classées en sept catégories, dont quatre peuvent être utilisées dans des matériaux métalliques, comme le montre la figure 3. L'une de ces catégories est appelée dépôt d'énergie directe (DED). Dans toutes les techniques qui y sont rassemblées, le matériau, au fur et à mesure qu'il est nourri, fond à travers la source d'énergie. Dans la technologie DED, le matériau peut être alimenté en deux formats: filetage ou poudre. L'utilisation de fil au lieu de poudre présente certains avantages: elle réduit le prix, augmente l'efficacité de l'utilisation du matériau et minimise les risques pour la sécurité et la santé au travail. En tant que source d'énergie pour la fusion du matériau, vous pouvez utiliser un laser, un faisceau d'électrons ou un arc électrique. En particulier, dans le processus de fabrication additive par fil et arc (wire arc additive manufacturing, WAAM) que j'ai étudié dans ma thèse, le matériau est alimenté en fil et fondu par un arc électrique.
Aujourd'hui, la technologie WAAM est devenue un processus de fabrication intéressant, car elle permet la fabrication de pièces métalliques de grande taille et de complexité géométrique moyenne à faible coût. En termes de caractéristiques, la technologie WAAM est semblable à un processus de soudage automatique: la source d'énergie fait fondre le fil à l'aide d'un arc électrique et, à travers le système de manipulation, place le métal fondu couche par couche sur le matériau de base jusqu'à la formation de la géométrie de destination.
Fil et arc
Selon la source de soudage utilisée, il existe différents types de processus WAAM. En effet, j'ai travaillé sur le processus WAAM basé sur la technologie de soudage à l'arc métallique protégé au gaz (GMAW), qui peut être intéressant pour une utilisation industrielle en raison des taux de productivité élevés (1-10 kg/h) qu'il obtient.
Dans la technologie GMAW (voir la partie droite de la figure 3), l'électrode consommable est le fil. C'est-à-dire que pour placer le matériau, un signal d'intensité est placé sur le fil et un arc électrique est formé entre le fil et la pièce. Cet arc électrique permet au métal de fondre et les gouttes de métal sont transférées du fil à la pièce. La figure 4 montre la corrélation entre le processus de formation des gouttelettes de métal fondu et le signal d'intensité.
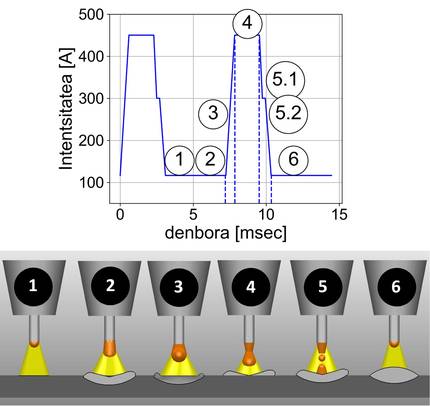
Ce transfert peut se produire de plusieurs façons: sous forme de jet, de forme globulaire ou de court-circuit. Au cours des dernières décennies, des sources de soudage avec des stratégies de contrôle à haute fréquence ont été utilisées pour contrôler le transfert des matériaux. Forme du signal d'intensité (forme d'onde, fréquence, etc.) appliquée au fil par ces stratégies de contrôle c'est ce qu'ils définissent. J'ai étudié dans ma thèse les modes de transfert existants pour les alliages d'acier et d'aluminium; j'ai constaté que les modes de transfert ont un impact significatif sur l'apport de chaleur à la pièce, ce qui conditionne à la fois la géométrie d'implantation et la productivité. J'ai également étudié l'effet des modes de transfert sur le degré de porosité atteint dans l'aluminium.
Enfin, la Figure 5 montre la voie à suivre pour la fabrication de pièces à partir de la conception initiale à travers le processus WAAM basé sur la technologie GMAW. Une fois que la conception est définie, la pièce est divisée en couches et des chemins de mise en œuvre sont créés pour chaque couche. Les paramètres du processus sont définis ci-dessous et la pièce est fabriquée par un robot ou une machine CNC. Pendant la fabrication, les paramètres internes du processus sont surveillés, ainsi que ceux des capteurs installés sur la machine. Le processus est contrôlé par des données surveillées en temps réel et enfin la pièce obtenue est mesurée pour s'assurer qu'elle est dans la tolérance.
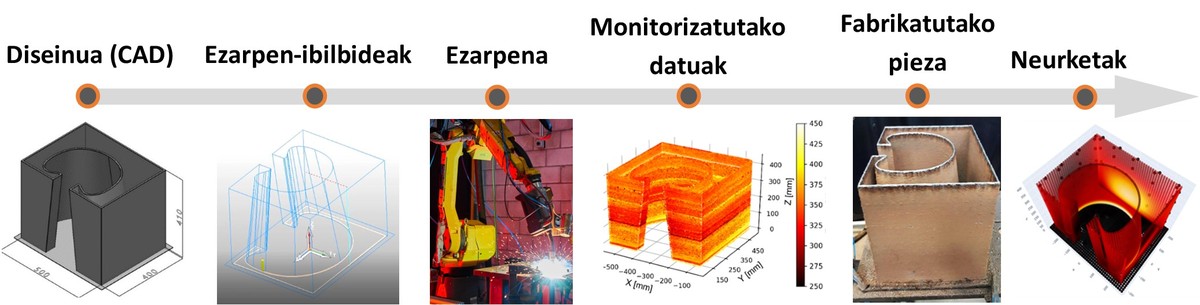
L'objectif principal de ma thèse a été de poser les bases pour que les machines puissent effectuer le parcours de la conception initiale à la pièce finale de la manière la plus autonome possible. Appuie sur un bouton et, comme les mains de Michel-Ange, le robot commence à fabriquer lui-même les pièces.
Bibliographie
Aldalur, E. Suárez, A., & Veiga, F. 2021. “Influence of Wire Arc Additive Manufacturing metal transfer modes on droplet formation, heat input, microstructure and porosity of as-built Al-Mg alloys”. Journal of Material Processing Technology, 2021, 297, 117271.
Cunningham, C. R., Flynn, J. M., Shokrani, A. Dhoki, V., & Newman, S. T... 2018. “Invited review article: Strategies and processes for high quality wire arc additive manufacturing». Additive Manufacturing, 22, 672–686.
Dilpoğlu, U. M., Gharehpapagh, B., Yaman, U. Dolen, M. 2017. “La fabrication additive dans l’ère de l’industrie 4.0.” Procedia Manufacturing, 11, 545–554.
General Electric. 2017. “GE Global Research, 3D Printing New Parts for Aircraft Engines”.
Herzog, D., Seyda, V. Wycis, E., & Emmelmann, C. 2016. “Additive manufacturing of metals”. Acta Materialia, 117, 371–392.
ISO/ASTM. ISO/ASTM 52900. 2015. Additive manufacturing - General principles - Terminology. International Standard, 5, 1–26.
Suárez, A., Aldalur, E. Veiga, F., Ciseaux, T., Tabernnero, I., & Nom, A. 2021. “Wire arc additive manufacturing of an aeronautic fitting with different metal alloys: From the design to the part.” Journal of Manufacturing Processes, 64, 1888-197.
Sun, C., Wang, Y. McMurtrey, M. D., Jerred, N. D., Liou, F., & Li, J. 2021. “Additive manufacturing for energy: "A review." Applied Energy, 282.
Williams, S. W., Martina F., Addison, A. C., Ding, J., Pardal, G., & Colegrove, P. 2016. “Wire + Arc additive manufacturing”. Materials Science and Technology, 32(7), 641–647.
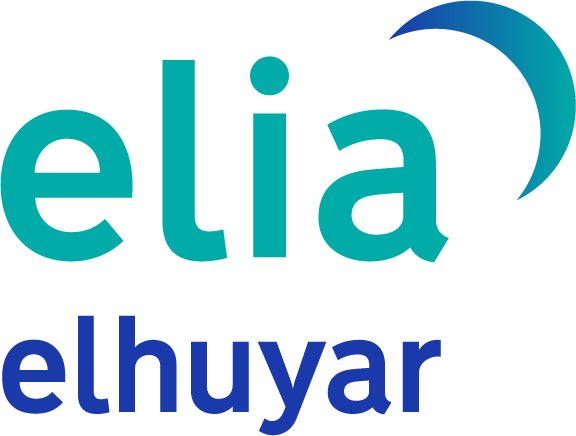