De quitar a engadir: apilando metais
2025/03/01 Aldalur Urresti, Eider - Tecnaliako ikertzailea, Ingeniaritza Mekanikoan doktorea Iturria: Elhuyar aldizkaria
Ao longo da historia, as tecnoloxías de fabricación e a industria en xeral foron evolucionando até chegar ás tecnoloxías de fundición, conformado e mecanizado que son hoxe en día os alicerces básicos da industria dos metais a nivel mundial. Os avances tecnolóxicos dos últimos anos fixeron necesario engadir a esta listaxe unha innovadora tecnoloxía de fabricación: a fabricación aditiva.
As pegadas dos primeiros instrumentos de pedra creados polo home nos retrotraen a 3,4 millóns de anos, á Idade de Pedra. Naquela época, o home comezou por primeira vez a traballar pedras, golpeándose uns contra outros para fabricar ferramentas, armas e puntas de aresta afiada mediante a extracción. Deste xeito, estableceuse o primeiro precedente das tecnoloxías actuais de mecanizado. A continuación, no Neolítico, deixouse de utilizar a pedra como elemento básico para a fabricación de artefactos e comezouse a traballar nos metais, primeiro mediante o martilleo en frío (precursor da conformación actual) e, posteriormente, mediante a fundición de minerais (precursor da fundición moderna).
Desde que o home colocou a primeira pedra do mecanizado moderno no Paleolítico, estas tecnoloxías de fabricación tiveron un gran desenvolvemento, como se observa na figura 1. Proba diso é, por exemplo, a impresionante escultura de 5,17 metros realizada polo gran escultor e pintor italiano Michelangelo Buonarroti entre 1501 e 1504. Para tallar esta obra, Miguel Ángel partiu dun denso bloque de mármore das canteiras de Carrara. A pesar dos anos, a fórmula segue sendo a mesma na tecnoloxía de fabricación máis utilizada na actualidade, no mecanizado. Hai cousas que permanecen inalterables.
Con todo, as tecnoloxías de fabricación foron as que experimentaron un maior desenvolvemento a partir de finais do século XVIII, grazas aos avances das revolucións industriais. Na fabricación do século XXI, as mans de Miguel Ángel foron substituídas polas máquinas e a automatización. Hoxe en día, dise que estamos na era da Industria 4.0. Os sistemas de produción intelixentes e as tecnoloxías da información intégranse nos sistemas industriais, e esta integración ciber-física xera fábricas intelixentes e de alta eficiencia que son capaces de fabricar produtos de alta calidade.
Cambio de paradigma
Do mesmo xeito que Miguel Ángel e aqueles primeiros seres humanos do Paleolítico, o proceso de fabricación de pezas por mecanizado parte dun bloque, ao que se lle quita o material obtense a forma final da peza. Na fabricación aditiva, pola contra, modifícase a paradigma de fabricación: a partir dun deseño dixital tridimensional (3D), engádese capa a capa a capa material, fabricando un obxecto físico (Figura 2).
A fabricación aditiva utilizouse por primeira vez en 1986, cando se creou a estereolitografía, tecnoloxía que utiliza os raios ultravioleta para formar os polímeros fotosensibles por capas. Orixinalmente, a fabricación aditiva tamén se denominou impresión 3D e desenvolveuse inicialmente para a fabricación de prototipos rápidos. Con todo, nos últimos anos produciuse un incremento na precisión, repetitividad e fiabilidade das técnicas de fabricación aditiva, e agora algunhas tecnoloxías de fabricación aditiva considéranse viables para a produción industrial. Actualmente, a fabricación aditiva pode producir pezas de alta consistencia nunha ampla gama de materiais como polímeros, metais, materiais cerámicos, composites, etc.
Este tipo de tecnoloxías prevese disruptivas que transformarán o tecido produtivo mundial e converteranse nunha ferramenta imprescindible para os diferentes sectores industriais. De feito, a fabricación aditiva responde o desenvolvemento do sistema produtivo que expón a Industria 4.0, xa que facilita o tránsito desde o deseño inicial até a peza final.
Por que engadilo?
Unha das principais vantaxes da fabricación aditiva é a capacidade de fabricar pezas de alta complexidade xeométrica. A utilización doutras tecnoloxías faría imposible este tipo de pezas, como pezas buxán, con detalles complexos ou con redes internas. A fabricación aditiva permite unha gran liberdade no deseño, o que resulta fundamental para aplicacións que requiren pouco peso, ou para que pezas que, se se fabrican con técnicas tradicionais, terían moitos compoñentes sexan dun só compoñente. Un exemplo coñecido é: A compañía General Electric instalou no seu motor de aviación CFM LEAP inyectores de combustible procedentes de fabricación aditiva, fabricados nun único bloque, un 25% máis lixeiros que o sistema de dezaoito compoñentes iniciais.
Ademais, a fabricación aditiva permite personalizar o produto final. Esta opción é limitada nas técnicas tradicionais de fabricación polo custo que supón. De feito, os moldes que se utilizan para a produción de pezas e o deseño dos utillajes teñen que ser modificados e o seu custo non é viable.Pola contra, a fabricación aditiva permite deseñar e fabricar pezas de forma directa, polo que é factible fabricar pezas únicas e personalizadas.
Por outra banda, mediante tecnoloxías de fabricación aditiva obtéñense pezas próximas á xeometría final, xa que o material se implanta só onde realmente é necesario. Así, a taxa de aproveitamento de materias primas é moi elevada (ver figura 2). Por iso, a fabricación aditiva pode ser unha opción competitiva para os materiais empregados (titanio, aliaxes de níquel, etc.). cando son caros, por exemplo na industria aeronáutica.
Por último, as tecnoloxías de fabricación aditiva demostraron ser moi axeitadas para reducir o consumo de enerxía, reducir o desperdicio de materiais e eliminar ou reducir os pasos de mecanizado. Por exemplo, nalgúns estudos obsérvase que o uso xeneralizado da fabricación aditiva reduciría nun 27% a demanda de enerxía.
Acumulando metais
Dentro da fabricación aditiva, cada tipo de tecnoloxía é unha combinación especial dunha fonte de enerxía, o formato do material a utilizar e un sistema móbil, e cada combinación serve para unha aplicación concreta. Segundo a terminología estándar creada pola asociación ASTM (Asociación de Probas e Materiais de Estados Unidos), as tecnoloxías de fabricación aditiva clasifícanse en sete categorías, das cales catro poden ser utilizadas en materiais metálicos, tal e como se mostra na figura 3. Unha destas categorías é a denominada deposición de enerxía directa (directed energy deposition, DED). En todas as técnicas que se recollen, o material fúndese a medida que se vai alimentando a través da fonte de enerxía. En tecnoloxía DED, o material pode ser alimentado en dous formatos: fíos ou po. O emprego da liña en lugar de po presenta vantaxes en canto a redución de prezo, aumento da eficiencia no uso do material e minimización dos riscos para a seguridade e a saúde no traballo. Como fonte de enerxía para fundir o material, pódese utilizar un láser, un feixe de electróns ou un arco eléctrico. En concreto, no proceso de fabricación aditiva por fío e arco que analicei na miña tese (wire arc additive manufacturing, WAAM) o material aliméntase como fío e fúndese cun arco eléctrico.
Na actualidade, a tecnoloxía WAAM converteuse nun interesante proceso de fabricación, xa que permite fabricar pezas metálicas de gran tamaño e de mediana complexidade xeométrica a baixo custo. En canto ás características, a tecnoloxía WAAM é similar a un proceso de soldadura automática: a fonte de enerxía funde o fío mediante un arco eléctrico e, mediante o sistema de manipulación, coloca o metal fundido sobre o material basee capa a capa até completar a xeometría do destino.
Fío e arco
Existen diferentes tipos de procesos WAAM en función da fonte de soldadura utilizada. De feito, eu traballei no proceso WAAM baseado na tecnoloxía de soldadura por arco metálico protexida por gas (gas metal arc welding, GMAW), que pode ser de interese para o seu uso na industria debido ás altas taxas de produtividade que alcanza (1-10 kg/h).
En tecnoloxía GMAW (ver figura 3 dereita) o cable é o electrodo consumible. É dicir, para a colocación do material establécese un sinal de intensidade no fío e fórmase un arco eléctrico entre o fío e a peza. Este arco eléctrico permite fundir o metal e transferir as pingas de metal do fío á peza. A figura 4 mostra a correlación entre o proceso de xeración das pingas do metal fundido e o sinal de intensidade.
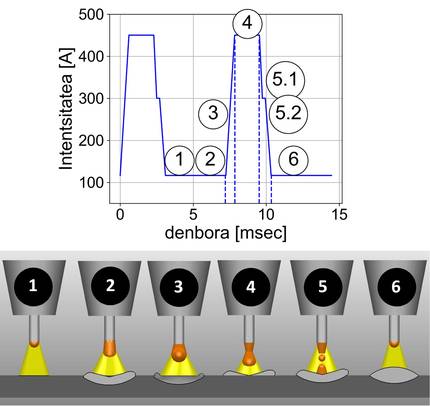
Esta transferencia pode producirse en forma de spray, de forma globular ou por circuítos curtos. Nas últimas décadas utilizáronse fontes de soldadura con estratexias de control de alta frecuencia para controlar a transferencia de material. A forma do sinal de intensidade aplicada ao fío por estas estratexias de control (forma de onda, frecuencia, etc.) definen. Na miña tese analicei as diferentes formas de transferencia para as aliaxes de aceiro e aluminio, observando que as formas de transferencia exercen unha influencia notable na achega de calor á peza, o que condiciona tanto a xeometría da implantación como a produtividade. Tamén analicei a influencia dos modos de transferencia no grao de porosidad que se consegue no aluminio.
Por último, a figura 5 mostra o camiño a seguir para a fabricación de pezas a partir do deseño inicial a través do proceso WAAM baseado en tecnoloxía GMAW. Unha vez definido o deseño, a peza divídese en capas e créanse as traxectorias de implantación de cada capa. A continuación defínense os parámetros do proceso e a peza fabrícase mediante un robot ou máquina CNC. Durante a fabricación se monitorizan os parámetros internos do proceso así como os dos sensores instalados na máquina. O proceso contrólase mediante datos monitorizados en tempo real e, finalmente, mídese a peza obtida para asegurar que se atopa dentro da tolerancia.
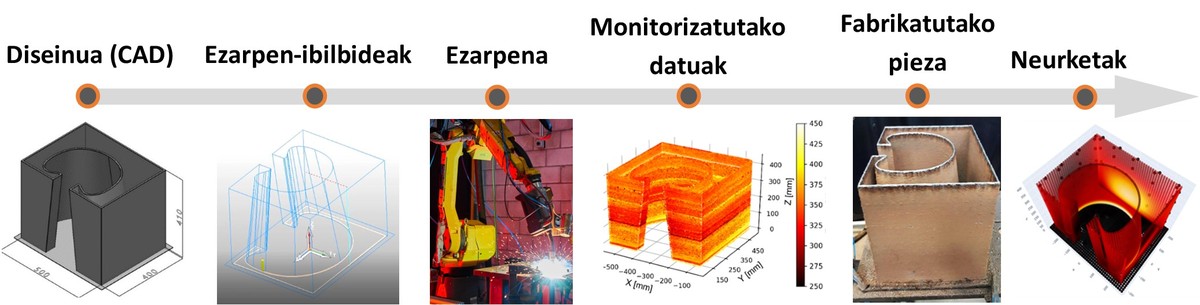
O obxectivo principal da miña tese foi sentar as bases para que as máquinas poidan percorrer da forma máis autónoma posible o percorrido desde o deseño inicial até a peza final. Dálle a un botón e que, como as mans de Miguel Ángel, o robot póñase a fabricar pezas pola súa conta.
Bibliografía
Aldalur, E., Suárez, A., & Veiga, F. 2021. “Influence of Wire Arc Additive Manufacturing metal transfer modes on droplet formation, heat input, microstructure and porosity of as-built Ao-Mg alloys”. Journal of material Processing Technology, 2021, 297, 117271.
Cunningham, C. R., Flynn, J. M., Shokrani, A. Dhokia, V. & Newman, S. T. 2018. “Invited review article: Strategies and processes for high quality wire arc additive manufacturing”. Additive Manufacturing, 22, 672–686.
Dilberoglu, U. M., Gharehpapagh, B. Yaman, U. Dolen, M. 2017. “The Role of Additive Manufacturing in the Era of Industry 4.0”. Procedia Manufacturing, 11, 545–554.
General Electric. 2017. “GE Global Research, 3D Printing New Parts for Aircraft Engines”.
Herzog, D., Seyda, V. Wycisk, E. & Emmelmann, C. 2016. Additive manufacturing of metals. Acta Materialia, 117, 371–392.
ISO/ASTM. ISO/ASTM 52900. 2015. Additive manufacturing - Xeral principles - Terminology. International Standard, 5, 1–26.
Suárez, A., Aldalur, E., Veiga, F., Artaza, T., Tabernero, I., & Lamikiz, A. 2021. “Wire arc additive manufacturing of an aeronáutic fitting with different metal alloys: From the design to the part”. Journal of Manufacturing Processes, 64, 188–197.
Sun, C., Wang, E., Murtrey, M. D., Jerred, N. D., Liou, F. & Li, J. 2021. “Additive manufacturing for energy: A review”. Applied Energy 282.
Williams, S. W. Martina, F., Addison, A. C., Ding, J. Pardal, G., & Colegrove, P. 2016. “Wire + Arc additive manufacturing”. Materials Science and Technology, 32(7), 641–647.
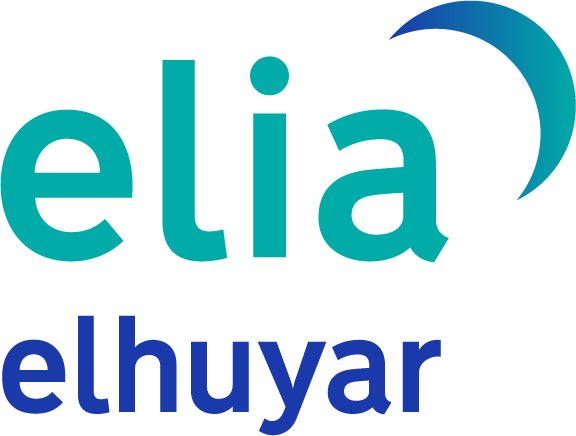