Turn+: Turning process, safer and more affordable
2025/04/08 Gorka Urbikain Pelayo - Gipuzkoako Ingeniaritza Eskola (EHU). CFAA Fabrikazio Aeronautiko Aurreratuko Zentroa (EHU). | Daniel Olvera Trejo - Institute of Advanced Materials for Sustainable Manufacturing, Tecnológico de Monterrey. Iturria: Elhuyar aldizkaria
Turning is a machining process that has been known since ancient times, but still faces great challenges with the development of new cutting processes, innovative kinematics and state-of-the-art tools. The main obstacle is the vibrations caused by the lack of rigidity of the part or tool (or one of them), which affects the productivity and quality of the parts. Although there are programmes, they are often expensive and require specific training. The Turn+ application, developed by the University of the Basque Country and Tecnológico de Monterrey as a simple and accessible decision making solution, offers the possibility of estimating key process data (such as forces, power, stability or roughness) in turning and boring processes.
The Turn+ application has been developed for the simulation and optimization of turning processes to predict both vibration and quality problems. Here’s how to work with this tool.
First, the initial parameters must be set (Figure 1):
- Type of tool and geometry: the application has different types of tools to choose from: round tip (circular, R), triangular (T), or rhomboidal (C, D, V). Each of them requires the definition of the variables Kr (position angle) and/or re (tip radius) corresponding to the geometry.
- Cutting coefficients (material): The cutting coefficients (Kf, Kn) reflect the mechanical strength, elasticity and/or flexibility of the material with respect to the tool. Theoretically, these parameters do not affect roughness versus stable cutting (in the theoretical formula of roughness, \(Ra = {f^2 \over 32r}\) where f is the advance and r is the radius of the plate). However, in flexible systems (very long tools, thin walls, etc.) the magnitude of the cutting forces, and therefore the coefficients, completely determines the vibration trend.
- Modes and type of turning (external or internal): Before running the Turn+ application, the modal parameters of the system must be obtained (for example, through impact tests). As it is organized, it will be very easy to take into account the three modal parameters: natural frequency, stiffness and damping rate. At the same time, it is necessary to define the type of turning: in our case, it is essential to choose between external (cylindrical) or internal (boring) turning. In principle, only the Z- and X-directional modes are considered in the analyses.
Once these three sets are configured, Turn+ is ready to start the simulations.
Functions of the Turn+ App
Once the initial parameters are properly defined, Turn+ initiates the dynamic simulation. The dynamic equations that govern the behavior of the system are solved in intervals of various rotational speeds (in abscissa) and cutting depths (in ordinate). Thus, by means of the Euler integration technique, the cutting forces are calculated in time taking into account the dynamic parameters, the cutting coefficients and the geometry of the tool. The acceleration, speed and position caused by the instantaneous cutting forces are continuously updated.
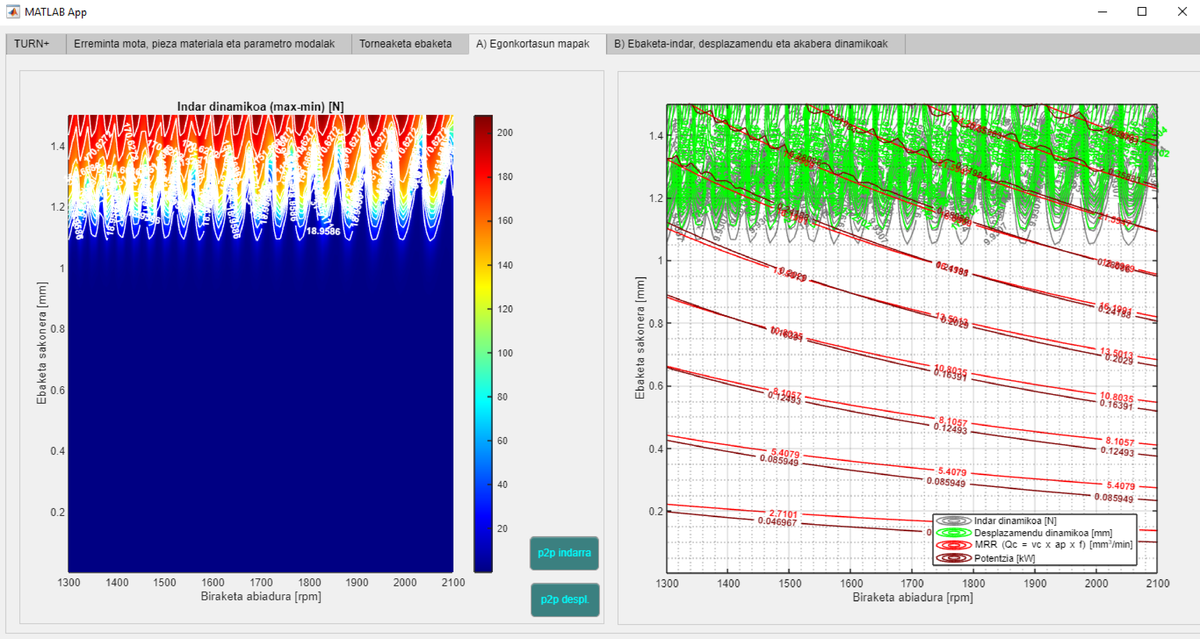
The threshold at which chatter vibrations are initiated is identified if, for a given speed of rotation, the difference between the maximum and the minimum of the dynamic forces becomes very sensitive as the depth of cut increases. When this occurs, it means that we have entered into a vibrating lobe, which marks the unstable cutting área. The diagrams do not provide an absolute limit of stability, but rather a trend or gradient to instability. For this reason, in conjunction with the lobe diagram, expressed in peak to peak dynamic forces (Figure 2, left), a multivariate diagram is also provided (Figure 2, right). It also indicates the isolates of dynamic forces, power, chip flow rate (MRR) and expected average roughness. In this way, the user has in a single map a summary of the estimates of the key process variables from the point of view of productivity and quality of the piece.
But Turn+ is not limited to this. It is also able to calculate the dynamic roughness for a specific case. First, the deviations (displacements) generated by the tool with respect to the theoretical trajectory during all periods (t, t+T, t+2T,...) are stored. With this position data, it is possible to form the tracking profile. Fig. 3 shows a specific case of external turning in which the tool vibrates in the Z direction.
This has direct implications for the surface roughness profile of the part. This case is indicating an unstable state in which both the cutting force and the vibration have a bad tendency. The range used to calculate the average roughness (Ra) (excluding the trantsitions) is plotted in green.
In this way, Turn+ offers the user a simple and easy to use interface to access the medium-high level during the turning process. It has a complete initial parameter configuration that includes data from the kinematic and dynamic geometry of the system, as well as detailed results about the most important variables. In this way, in the new era of digital turning, Turn+ can become a valuable tool for both learning and industry decision-making.In fact, this app completes the path started with Mill+.
The bibliography
[1] G. You're in Urso, L.N. By López de Lacalle, F.J. In Camp, A. Assisted by Fernández, A. Elías, Stability prediction in straight turning of a flexible workpiece by collocation method, International Journal of Machine Tools and Manufacture, Vol. 54–55, 2012.
[2] G. Urexcellent,Predicting stability in turning processes by the method of colocation by polynomials of Chebyshev, PhD thesis, University of the Basque Country, UPV-EHU, 2014.
[3] J.A. House in Palacios, D. Assisted by Olvera, G. You're looking great, A. Assisted by Elias-Zúñiga, O. Martínez-Romero, in L.N. Presented by López de Lacalle, C. Assisted by Rodríguez, H. Martínez-Alfaro, Combination of simulated annealing and pseudo spectral methods for the optimum removal rate in turning operations of nickel-based alloys, Advances in Engineering Software, Vol. 115, 2018.
[4] G. It's great, D. Olvera, Mill+: stable and quality milling tool, Elhuyar, 09/12/2024.
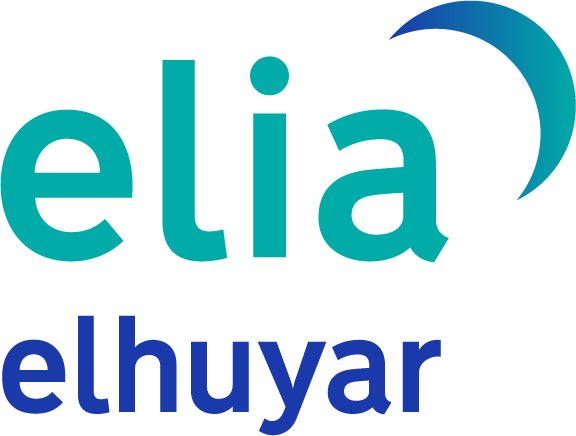
Gai honi buruzko eduki gehiago
Elhuyarrek garatutako teknologia