Water saws
1990/07/01 Azkune Mendia, Iñaki - Elhuyar Fundazioa Iturria: Elhuyar aldizkaria
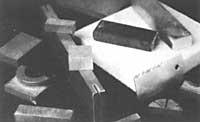
Since they are able to cut any material, we do not think it is inappropriate to say that these machines are water saws, although at first it seems something else, but we realize the birth and diffusion of this technique.
In 1968, scientist Norman Franz patented the technique of cutting high pressure waterjet materials in North America, and three years later, an industry to develop this technique. The first investigations were carried out in the field of aeronautics and soon the automotive one was also addressed. In fact, car manufacturers needed tools that cut composites without altering their internal molecular structure.
The success of the warm water jet has been enormous. Today, for example, more than 1,500 machines of this type work in the world and more than five hundred in Europe. In Europe Sweden and the German Federal Republic began to use this technique and later spread to France. In Sweden, for example, the company Karman produces wooden and cardboard puzzles with water jet.
Machines are governed by numerical controls and computers, making sure that there are no two identical pieces in the puzzle. In addition, this system has the advantage that the cut pieces are mounted in the puzzle itself. Therefore, it is no surprise that this Swedish company is a world leader in puzzles and wants to extol the waterjet technique.
Opened in France in early 1988, the first water saws center has been requested by numerous companies. They cut anything: apples, cheeses, concrete, steel, glass, wood, marble or composite. The 35 mm thick anti-whale glass, for example, is cut by a thin stream of water like paper. What the bullets can't do is the water jet.
The basis of the technique is very simple. The fine water jet is projected at a very high speed. The speed ranges from 600 to 900 meters per second, two or three times higher than that of sound. For water to reach this speed, however, it must be compressed at pressures of between 2,000 and 5,000 bars, something that can not get anyone. In the kitchen of the house, for example, the water only has a pressure of about three bars.
The water used in the machine must be clean. Lime, minerals and other impurities from water are removed to prevent deterioration of circuit parts. Water is filtered and additional materials are added.
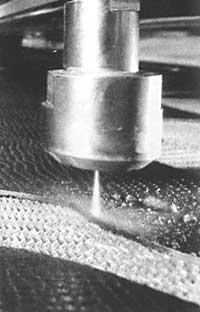
Once the water is conditioned, first a pump applies a pressure of about ten bars, where it passes to a high pressure pump. A large hydraulic piston pushes it to a small piston with a pressure of 4,000 bar.
High pressure water flows to the end through stainless steel pipes. The tubes are of small diameter and large wall thickness and the ends are of very hard material, such as sapphire. The orifice of the ends or injectors is usually of different diameter depending on the type of material to be cut and the thickness.
Normally the internal diameter of the injectors is 12, 18, 25 and 35 centimeters (therefore, the diameter of the water jet). At a pressure of 2.000 bar, the water exits at 640 m/s, if the pressure is 3000 bar, the exit velocity of the water is 770 m/s and 4000 bar at 900 m/s. In other words, the speeds are 2,300, 2,800 and 3,200 km/h.
At such incredible speeds water does not wet the matter it passes through. For example, a fiberglass plate can be cut very quickly (more than 100 meters per minute) without getting wet.
Another great advantage of water jet is being able to work cold. Therefore, the pieces that are worked are not heated or their material structure is modified. For example, when laser cutting parts, this advantage does not exist. The laser cuts the roasted pieces and leaves them the black edges. For example, when the steel is cut, the grains of the structure of the material with laser melt and in some cases this is harmful, as in the case of tempered steel. The water jet does not cut like this. The first particles of material are displaced and subsequently extracted. Somehow, it is a sudden wear that occurs with these water saws.
Another advantage of this cutting technique is that a single machine can feed many jets (for example, up to eight). Instead, each ray needs its full equipment.
Both the laser and the water jet save a lot of material as the chips that rise in other systems do not come out. The cutting line is very narrow and material is hardly lost.
It seems that the jet when working at these pressures and speeds has to spend a lot of water, but it is not so. Pressures range from 2.5 to 0.4 liters per minute. Therefore, a maximum of 240 hours. It is recommended to decant the water used before pouring it into the sewer as it is not suitable to pour contaminated water.
Depending on the composition of the jet, three types can be considered. Pure water, water mixed with polymer or water mixed with abrasive material is used depending on the type of material to be cut. When it comes to a soft and fine material, enough water to cut. However, to cut thick pieces, polymers are mixed into the water.
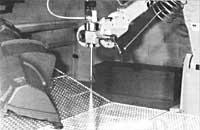
Polymers improve the molecular coherence of water, allowing further work of the injector. For example, from about twenty centimeters high the jet is mixed air and 70 centimeters from the injector the jet is replaced by water vapor. By mixing the water with 3% polymer, the body of the jet does not melt so fast, since the water is more conflictive.
Another option is to mix abrasives into water. This system is used to cut hard materials such as steel, granite, marble and titanium. Although quartz abrasives are mixed with water, the cut edge is clean and burr-free.
However, one of the most useful advantages of waterjet cutting is its ease of automation. In the current era of flexible production cells, water jet is a perfect system. In automotive, for example, the cutting die of the control panel inside the car has an approximate cost of twenty million pesetas. This is a very important expense, but can be easily amortized with large series of cars. Today, however, car models are changing faster and the amortization of expensive hydraulic press dies is not so easy.
In addition, the same car model currently has many variants for the buyer to have more possibilities, which also involves changing die. With the water jet all these problems are easily solved. A numerical control program governs the water jet and if there are changes in the part to be cut, simply place a program that is collected on the computer. Water jets are therefore suitable for use in flexible manufacturing cells and hydraulic press dies are not expensive.
The water saw also seems very suitable for use in electronics, especially for cutting printed circuit boards. In food, let's not say. Water jet is the only neutral cutting instrument. On the other hand, researchers are conducting cutting sessions with iced water. Keep in mind that at 3,000 bars of pressure water does not freeze at 0°C, but at about -15°C. Therefore, they want to keep the water under pressure at -10°C and, just outside the injector, it will freeze in free atmosphere. So the ice will cut the piece.
In the equipment for the use of this technique it can be said that two elements are particularly important: pumps and injectors. The Bertin house has improved its pumps and injectors to obtain a pressure of 7,000 bars, obtaining a duration ten times longer than the initial.
Another capacity of the water jet is to be able to cut overlapping plates of equal or different thickness and / or weight. This way you can cut more than one piece each time. In addition, the shape of the piece can be any. A marble plate can be cut into a dog, for example, or shaped into a tree.
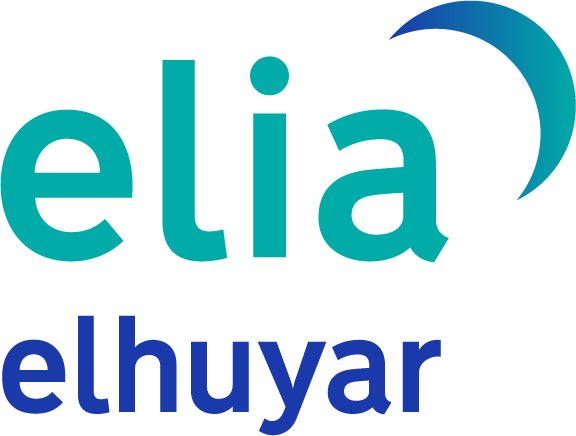
Gai honi buruzko eduki gehiago
Elhuyarrek garatutako teknologia